In the fast-paced world of automotive manufacturing, efficiency, durability, and cost-effectiveness are paramount. One process that has gained significant traction in meeting these demands is aluminum blanking. This method involves cutting flat pieces of aluminum sheet metal into specific shapes, an essential step in the production of various aluminum automotive components. But what makes aluminum blanking so popular in the automotive industry? Let’s delve into the reasons behind its widespread adoption.
What Is Aluminum Blanking?
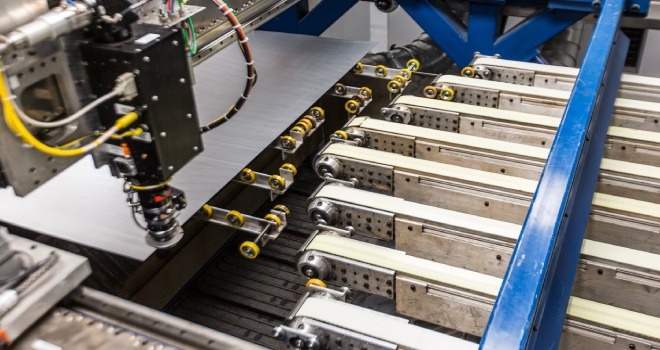
Aluminum blanking is a manufacturing process that involves cutting flat pieces of aluminum sheet metal into specific shapes or blanks. These blanks are then further processed to create various components used in different industries, including the automotive sector. The blanks are typically cut using specialized tools like dies or punches to achieve the desired shapes with precision and accuracy. Aluminum blanking is favored for its versatility, allowing manufacturers to produce customized parts that meet specific requirements for different applications.
Aluminum Blanking Types
Configured Blanking: Configured Blanking, also known as “peripheral” or “cookie cutter” blanking, involves feeding a rectangular blank or coil into a specialized press with a stamping die engineered to shape the part’s periphery accurately. This method is tailored for producing precise and complex shapes with optimal material utilization. It is commonly used for manufacturing automotive components like fenders, bodysides, and doors.
Laser Blanking: Laser Blanking is a modern technique that utilizes a high-power laser to cut 2D shapes from pre-cut blanks or coils fed into the cutting cell. This method offers flexibility in shaping various parts and has seen advancements in cutting speed and throughput with the incorporation of multiple cutting heads. While the initial cost of laser blanking lines is high, the increasing throughput is driving down the relative cost per produced blank, making it a versatile and efficient option for aluminum blanking processes.
Aluminum Automotive Components
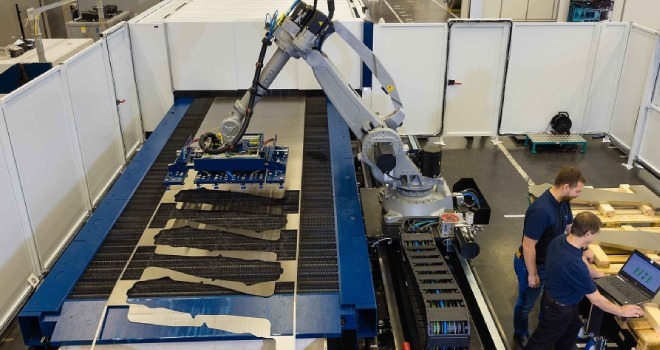
Aluminum stands as a cornerstone material in the automotive industry, playing a pivotal role in crafting a diverse array of essential components. From doors to hoods, fenders, radiators, suspension parts, and structural elements, the utilization of aluminum in these automotive components offers a spectrum of benefits that elevate performance and design standards.
-
Doors: Aluminum is preferred for automotive doors due to its lightweight nature, which reduces vehicle weight and enhances fuel efficiency. Additionally, aluminum’s strength ensures structural integrity and safety, while its corrosion resistance prolongs the door’s lifespan.
-
Hoods: Aluminum hoods offer a combination of strength and weight savings, contributing to improved vehicle performance. The material’s corrosion resistance and formability allow for aerodynamic designs, enhancing both efficiency and aesthetics.
-
Fenders: Aluminum fenders benefit from the material’s corrosion resistance and formability, allowing for intricate designs that enhance vehicle aesthetics. The lightweight properties of aluminum fenders contribute to improved handling and fuel efficiency.
-
Radiators: Aluminum’s excellent thermal conductivity makes it ideal for radiators, ensuring efficient heat dissipation and optimal cooling system performance. The material’s corrosion resistance also helps maintain the radiator’s functionality over time.
-
Suspension Components: Aluminum suspension components offer a balance of strength and weight reduction, improving vehicle handling and performance. The material’s durability and resistance to corrosion ensure longevity and reliability in various driving conditions.
-
Structural Components: Aluminum structural components provide high strength-to-weight ratios, crucial for vehicle safety and performance. The material’s formability allows for complex structural designs that enhance rigidity and crashworthiness, contributing to overall vehicle safety.
Benefits of Aluminum Blanking for Automotive Parts
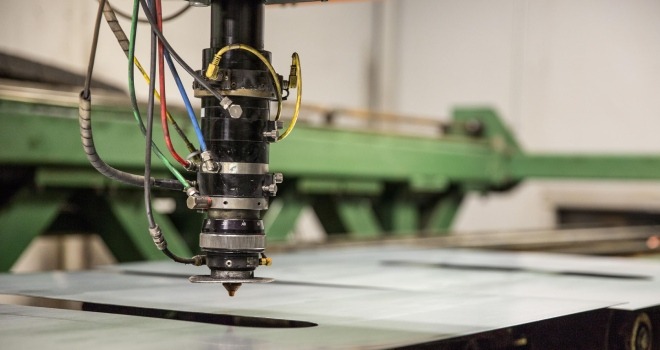
The utilization of the aluminum blanking process for manufacturing automotive components offers a range of advantages that align with the stringent requirements of the automotive industry. Here’s why the aluminum blanking process is preferred for crafting these components:
Precision and Accuracy: Aluminum blanking ensures precise and accurate cutting of flat aluminum sheets into specific shapes or blanks. This precision is crucial for creating intricate and custom-designed aluminum automotive components that meet exact specifications.
Material Efficiency: The blanking process optimizes material usage by minimizing waste. This efficiency is particularly beneficial when working with aluminum, an alloy that can be relatively expensive compared to other materials used in automotive manufacturing.
Formability: Aluminum is highly formable, enabling it to be easily shaped and molded into complex designs during the blanking process. This formability allows for the creation of lightweight yet strong components that are essential for enhancing vehicle performance.
Weight Reduction: Aluminum’s lightweight nature contributes to overall weight reduction in vehicles, leading to improved fuel efficiency and better handling. The aluminum blanking process helps maintain these weight-saving advantages by ensuring precise shaping and cutting of components.
Advancements in Aluminum Blanking Technology
Advancements in aluminum blanking technology within the automotive industry are propelling a wave of innovation, reshaping the production of lightweight, high-performance components. These technological strides are revolutionizing how automotive parts are manufactured, offering a plethora of benefits to manufacturers and consumers alike.
Industry 4.0 Integration: Integration of Industry 4.0 technologies such as IoT (Internet of Things), AI (Artificial Intelligence), and machine learning to optimize and automate the aluminum blanking process. This includes real-time monitoring, predictive maintenance, and data analytics for improved efficiency.
Advanced Laser Cutting Systems: Continued advancements in laser cutting systems with higher power, increased cutting speeds, and improved accuracy for laser blanking applications. This can lead to enhanced productivity and cost-effectiveness.
Robotics and Automation: Greater integration of robotics and automation in aluminum blanking processes to streamline operations, increase throughput, and improve consistency in part production.
Multi-Material Blanking: Development of technologies capable of blanking multiple materials, including aluminum alloys and composites, in a single process. This can cater to the growing trend of using hybrid materials in automotive manufacturing.
Smart Die Technologies: Implementation of smart die technologies with sensors and actuators for real-time adjustment of cutting parameters, improving part quality and reducing setup times.