Aluminum is a versatile metal known for its lightweight properties, corrosion resistance, and ease of fabrication. When it comes to bending aluminum, the choice of alloy plays a crucial role in determining the success of the bending process. Various aluminum alloys exhibit different characteristics, making some more suitable for bending than others. In this blog post, we will explore some of the best aluminum for bending applications.
What Factors Affect Aluminum Bending?
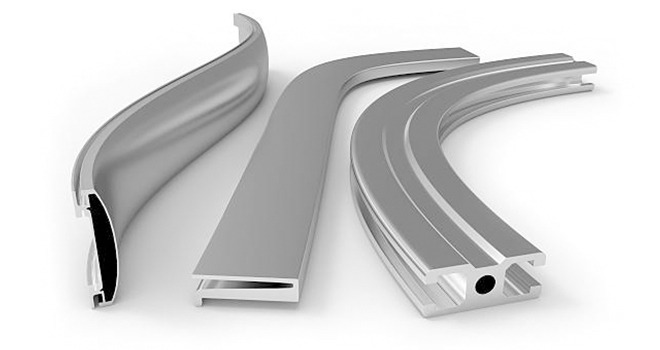
Three key elements influence the bendability of aluminum alloys: the alloy’s formability, the thickness and bend radius, and the percent elongation.
Aluminum Formability
Formability refers to a material’s capacity to undergo permanent deformation without cracking or tearing during the forming process, also known as plastic deformation in materials science. Higher strength in an aluminum alloy typically translates to increased difficulty in bending due to the trade-off between strength and elongation (ductility), where one increases as the other decreases. Understanding aluminum alloys is crucial when selecting the appropriate material. Aluminum alloys are designated into various series with distinct chemical compositions tailored for diverse applications in metal processing.
Formability Of Different Aluminum Series
- Series 1xxx: Comprising 99.00% pure aluminum, these alloys offer minimal structural value, high ductility in the annealed state, and excellent corrosion resistance.
- Series 2xxx: Aluminum-Copper alloys known for excellent machinability, limited cold formability (except when annealed), and lower corrosion resistance, often requiring anodization before use.
- Series 3xxx: Aluminum-Manganese alloys, containing 1% Manganese, retain good ductility, corrosion resistance, and formability, making them ideal for forming applications.
- Series 4xxx: Aluminum-Silicon alloys, featuring silicon additions to lower the melting point, primarily used in welding wire manufacturing.
- Series 5xxx: Aluminum-Magnesium alloys offering a balance of high strength, corrosion resistance, formability, and weldability.
- Series 6xxx: Aluminum-Magnesium-Silicon alloys, heat treatable with strong, corrosion-resistant, and easily formable properties, commonly employed in architectural uses.
- Series 7xxx: Aluminum-Zinc-Magnesium and Aluminum-Zinc-Copper alloys, renowned for high strength but challenging formability due to their strength characteristics.
Thickness And Bend Radius Of Aluminum
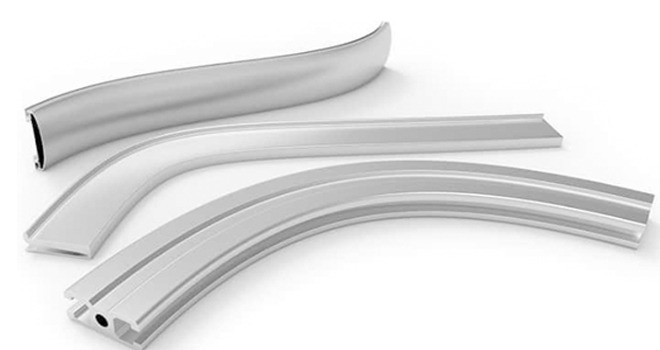
Attempting to bend aluminum to a small radius poses the risk of tearing or cracking, especially when trying to achieve tight angles without compromising the material’s integrity.
What Is The Minimum Bend Radius For Aluminum?
In the realm of aluminum bending, the minimum bend radius guideline typically stands at 1.5 times the thickness for thicker aluminum sheets. However, for 0.5-inch-thick aluminum, this threshold rises to about 2 times the material’s thickness. It’s worth noting that as the material hardness increases, so does the minimum required bend radius.
Percent Elongation Of Aluminum
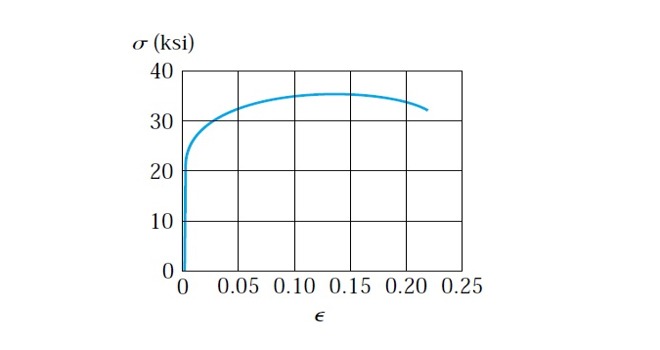
Percent elongation in aluminum signifies its ability to undergo plastic deformation under tension, denoting its ductility beyond the yield strength limit. Ductile aluminum alloys can sustain significant plastic deformation with minimal stress increments, enhancing their bendability. A critical factor to assess is an alloy’s formability, determined by the elongation percentage and the variance between yield and ultimate tensile strengths.
A fundamental principle states that alloys with higher elongation values (resulting in a broader range between yield and tensile strengths) exhibit superior forming capabilities.
Considering the alloy descriptions and the data, it becomes evident that series 3xxx, 5xxx, and occasionally 6xxx stand out as optimal choices for forming and bending applications. On the contrary, series 2xxx and 7xxx should be avoided due to their exceptional strength, making them challenging to form effectively.
Best Aluminum For Bending
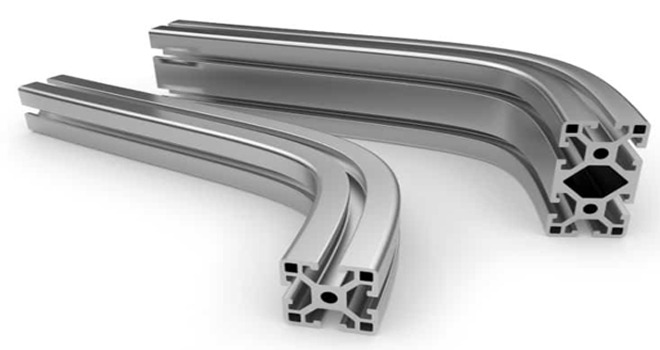
3003 Aluminum
In most applications, this is the best aluminum for bending. 3003 aluminum is distinguished by its remarkable formability, allowing for bending without the requirement of heat. This versatile alloy is commonly employed in applications such as gutters, roofing, siding, chemical equipment, and storage tanks. With medium strength, excellent cold workability, a 25% elongation capacity, and a significant 14 Ksi gap between its yield and tensile strengths, 3003 aluminum proves to be a reliable choice across a range of industrial uses.
5052 Aluminum
Featuring impressive elongation properties, this aluminum grade stands out as the second option for aluminum bending applications. With its magnesium-enriched composition, 5052 aluminum presents a blend of commendable bendability and moderate-to-high strength. This alloy is well-suited for applications involving hydraulic tubes, traffic signs, medical equipment, marine components, and electronics. Noteworthy for its 20% elongation capability, a 21.5 Ksi divergence between yield and tensile strengths, and exceptional resistance to corrosion, 5052 bending aluminum stands out as a versatile choice across various industries.
6061 Aluminum
Famed for its remarkable strength, 6061 aluminum, while marginally less flexible than 3003 and 5052, is a stalwart in various industries. This alloy finds extensive application in structural and construction projects, as well as in the manufacturing of food containers, aerospace components, automotive parts, and more. Despite being the strongest option, 6061 aluminum boasts an 18% elongation capacity and a 10 Ksi disparity between yield and tensile strengths in its annealed state, rendering it suitable for bending tasks. Yet, exercising caution is advised when bending the T4 and T6 tempers due to their reduced flexibility.