A360 aluminum, a favored die casting alloy, excels in manufacturing for its unique properties. Discover how this alloy elevates die casting processes.
A360 Aluminum Overview
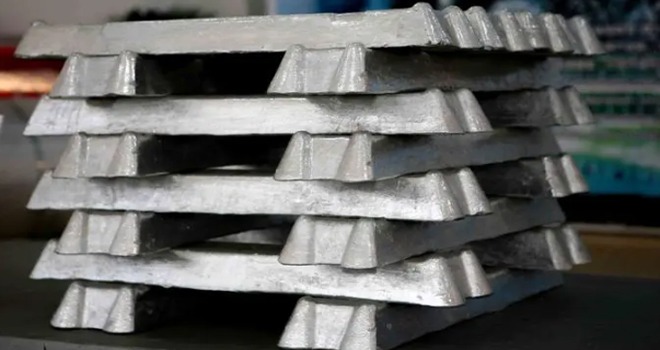
A360 Aluminum, a part of the number 3 series of aluminum alloys, is renowned for its exceptional fluidity and resistance to hot cracking. Comprising mainly aluminum, silicon, and trace elements, the presence of silicon significantly enhances its casting properties, making it a favored choice in various casting processes.
Historically, A360 Aluminum has found applications in industries requiring high thermal and electrical conductivity. Its unique composition enables excellent machinability, corrosion resistance, and surface finish, offering a balanced blend of mechanical properties and production ease compared to other aluminum alloys.
A standout feature of A360 Aluminum is its versatility in die casting, gravity casting, and other molding techniques, making it ideal for intricate shapes and thin-walled components commonly seen in automotive, lighting, and technological applications. Being a part of the 3xx.x alloy series, A360 is predominantly alloyed with silicon, making it a popular choice for die castings within this series.
A360 Aluminum Chemical Composition
Copper (Cu) | Iron (Fe) | Magnesium (Mg) | Manganese (Mn) | Nickel (Ni) | Silicon (Si) | Tin (Sn) | Zinc (Zn) |
≤0.6% | ≤1.3% | 0.4-0.6% | ≤0.35% | ≤0.5% | 9.0-10.0% | ≤0.15% | ≤0.5% |
The chemical composition of A360 Aluminum is carefully balanced to optimize its properties for die casting applications. Silicon, the primary alloying element present in a range of 9.0-10.0%, enhances fluidity, facilitating smooth flow into intricate molds during die-casting. This higher silicon content not only aids in fluidity but also bolsters the alloy’s resistance to corrosion.
Copper content in A360 is kept minimal, below 0.6%, to improve corrosion resistance while moderating hardness and tensile strength. To compensate for these reductions, magnesium is included in controlled amounts, typically ranging from 0.4% to 0.6%. This intricate alloy formulation ensures that A360 Aluminum maintains a delicate balance of properties, making it a preferred choice for applications requiring both intricate detailing and resistance to corrosion.
A360 Aluminum Mechanical Properties
Hardness, Brinell | Tensile Strength,Ultimate / Mpa | Tensile Strength, Yield / Mpa | Elongation % in 2in |
75 | 317 | 165 | 3.5 |
These properties indicate that A360 Aluminum offers moderate hardness, with a respectable ultimate tensile strength of 317 MPa and a yield strength of 165 MPa. The elongation percentage in a 2-inch (51mm) specimen is 3.5%, suggesting a degree of ductility in the material. This combination of properties makes A360 Aluminum suitable for applications where a balance of strength and formability is required.
A360 Aluminum Physical Properties
The physical properties of A360 Aluminum emphasize its thermal and electrical conductive capabilities:
Thermal Conductivity: A360 Aluminum exhibits a high thermal conductivity of 113 W/m °K, indicating its efficiency in transferring heat.
Electrical Conductivity: With an electrical conductivity of 21% IACS (International Annealed Copper Standard), A360 Aluminum demonstrates its ability to conduct electricity effectively.
A360 Aluminum Casting Methods
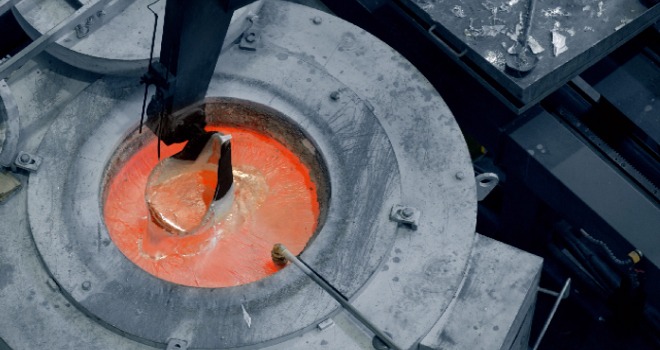
A360 Aluminum employs both die casting and gravity casting methods due to their distinct advantages and suitability for varying production needs:
Die Cating A360 Aluminum
The high-pressure die casting method is chosen for A360 Aluminum due to its ability to create intricate shapes with precise detail. A360’s exceptional fluidity and resistance to hot cracking make it an excellent fit for die casting, resulting in strong and visually appealing parts that meet stringent quality standards.
Gravity Casting A360 Aluminum
Gravity casting is utilized for A360 Aluminum to produce larger components in a simpler and cost-effective manner. This method is preferred when intricate details are not required, making it ideal for bulkier parts. A360’s unique composition ensures a smooth surface finish and reliable mechanical properties, making it a practical choice for applications where strength and cost efficiency are priorities.
A360 Aluminum vs. A380 Aluminum
A380 Aluminum is widely popular in casting, but A360 Aluminum stands out for its unique benefits. The key contrast lies in A360’s reduced copper and increased silicon content. This composition gives A360 improved corrosion resistance and elevated temperature strength compared to A380. While these differences are significant, both alloys share many comparable properties. A380 remains favored for its extensive casting applications, while A360 excels in areas demanding heightened resistance to corrosion and strength at elevated temperatures.
A360 Aluminum Applications
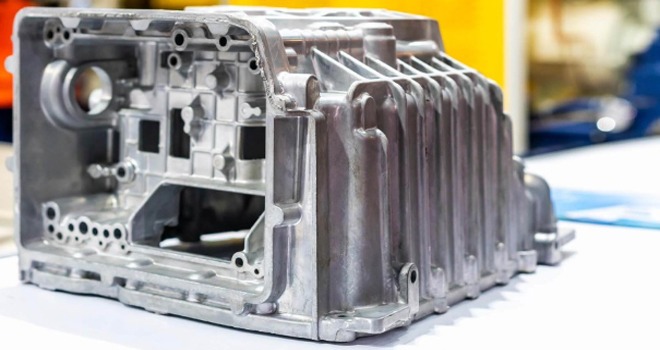
A360 Aluminum finds diverse applications across various industries:
Automotive Applications
A360 Aluminum is extensively utilized in the automotive sector for its exceptional strength-to-weight ratio and corrosion resistance. It is commonly employed in engine components, transmission parts, and structural elements of vehicles, contributing to fuel efficiency and long-term durability.
Lighting Applications
In the lighting industry, A360 Aluminum’s thermal conductivity and malleability are highly valued. It is commonly used in LED light housings and heat sinks to enhance heat dissipation, prolonging bulb lifespan. Its corrosion resistance ensures longevity, even in challenging environments, while its lightweight nature facilitates easy installation in modular lighting systems.
Electronic Applications
A360 Aluminum is preferred in electronic applications due to its combination of visual appeal and functional advantages. Its sleek finish enhances the aesthetics of devices such as laptops and smartphones, while its thermal properties facilitate effective cooling, leading to improved performance and durability. Additionally, the alloy’s structural strength is utilized in constructing sturdy frames for servers and other high-performance tech equipment.