Aluminum, a versatile and lightweight metal, undergoes a captivating metamorphosis during the rolling process. Whether crafted into sheets, plates, or foils, rolled aluminum embodies a coveted blend of strength, lightness, and resilience. This versatility renders it indispensable across a spectrum of applications, from food packaging and high-speed railways to industrial printing and fuel-efficient aircraft.
What Is Aluminium Rolling?
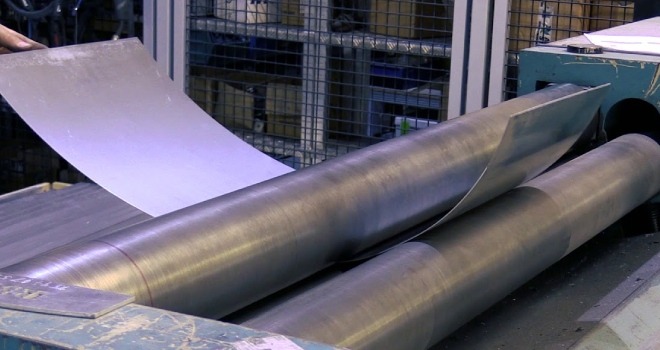
Aluminium rolling is a manufacturing process that involves passing aluminum ingots through a series of rollers to reduce their thickness and create uniform sheets or foils. This method is crucial for shaping aluminum into various forms used across industries. By subjecting the metal to high temperatures during hot rolling and further processing at room temperature through cold rolling, aluminum can be tailored to specific dimensions and properties. The process enhances the metal’s mechanical properties, making it ideal for applications requiring strength, lightness, and durability.
Aluminium Rolling Methods
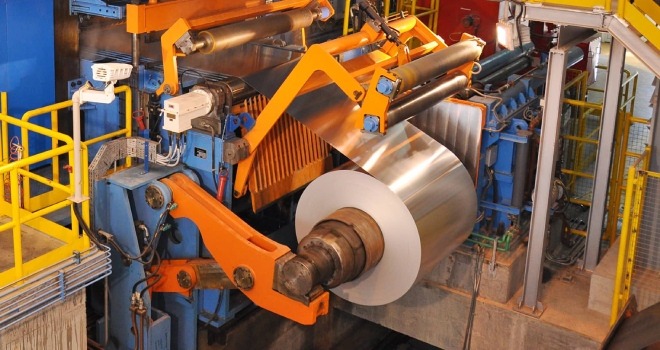
Aluminum rolling involves two primary methods: cold rolling and hot rolling.
Aluminum Cold Rolling
Cold rolling is a process where aluminum is passed through rollers at room temperature to achieve precise thickness and surface finish. This method enhances the material’s mechanical properties and dimensional accuracy. Cold-rolled aluminum is often used in applications requiring tight tolerances and a smooth surface finish.
Aluminum Hot Rolling
Hot rolling involves passing aluminum through rollers at elevated temperatures. This process reduces the material’s thickness and enhances its mechanical properties. Hot-rolled aluminum is typically softer and more malleable than cold-rolled aluminum. It is commonly used in applications where formability and ductility are essential.
Aluminium Rolling Process
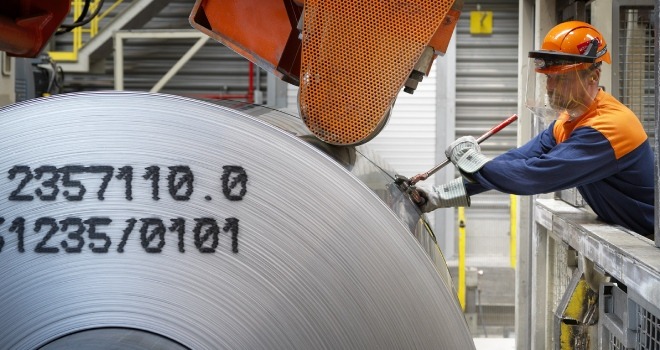
Step 1: Initial Aluminium Processing
The aluminium rolling process commences with the initial aluminum processing stage. Here, the aluminum rolling mill receives aluminum slabs or billets to prepare them for the rolling process. The decision to heat the stock or not is crucial and depends on the desired material properties for the operation.
When aluminum undergoes rolling without preheating, it experiences cold working. This process enhances the metal’s strength by altering its microstructure but also increases its brittleness. Conversely, if the aluminum is heated in the mill, it is referred to as hot working. The specific temperature range for hot working varies depending on the aluminum alloy being processed, allowing the metal to maintain its ductility by preventing or minimizing work hardening.
Step 2: Thickness Reduction Process
Following the initial processing stage, aluminum slabs are passed through a series of roller mills with decreasing separation between them. Pressure is applied from the top and bottom of the slab in these roller mills, gradually reducing its thickness until the desired gauge is achieved.
Depending on the final thickness obtained, the rolled aluminum product is categorized into three main types as defined by the Aluminum Association, each serving specific purposes:
- Aluminum Plate: Aluminum rolled to a thickness of 0.25 inches (6.3 mm) or more is known as aluminum plate, commonly used in aerospace applications such as aircraft wings and structures.
- Aluminum Sheet: Ranging between 0.008 inches (0.2 mm) and 0.25 inches (6.3 mm) in thickness, aluminum sheet is a versatile form of rolled aluminum used in various industries like beverage and food packaging, signage, and automotive components.
- Aluminum Foil: Aluminum rolled to a thickness less than 0.008 inches (0.2 mm) is categorized as aluminum foil, widely employed in applications like food packaging, building insulation, and vapor barriers.
Step 3: Post-Rolling Processing
After the thickness reduction process, rolled aluminum products may undergo additional processes such as blank cutting and hot forming. In some instances, shaping can be integrated into the rolling process for specific geometries like architectural siding or roofing sheets using specially designed rollers.
Chemical or mechanical surface treatments, such as anodization and PVDF coating, may be applied at the end of the process. These treatments can alter the appearance, enhance properties like corrosion resistance, or texture the surface of the product, providing a refined finish to the rolled aluminum.
The Mill For Aluminum Rolling
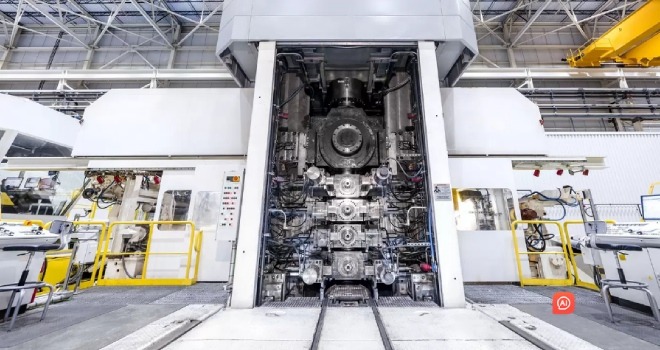
In the realm of aluminium rolling, different types of mills are employed to cater to the diverse needs of producing various aluminum products. Understanding these aluminum rolling mills and their suitability for specific aluminum products is crucial in the manufacturing process. Let’s delve into the different types of mills commonly used:
Reversing Mill
A reversing mill is a common type of mill used in aluminium rolling processes. This mill has the capability to roll in both directions, allowing for increased flexibility in shaping and forming aluminum sheets. Reversing mills are often used for producing aluminum sheet and plate products due to their versatility in thickness reduction.
Tandem Mill
Tandem mills consist of several stands of rolling mill rolls arranged in succession. Each stand reduces the thickness of the aluminum material further, providing precise control over the final product’s dimensions. Tandem mills are ideal for high-volume production of aluminum sheet and foil products.
Cold Rolling Mill
Cold rolling mills are specifically designed to work with cold-rolled aluminum sheets. These mills operate at room temperature or slightly below, allowing for the production of thinner and more precise aluminum products. Cold rolling mills are commonly used for producing aluminum foil and sheet products.
Hot Rolling Mill
Hot rolling mills are designed to work with aluminum at elevated temperatures. This process is suitable for shaping aluminum into various forms without cracking or brittleness. Hot rolling mills are often used to produce thicker aluminum plate products used in aerospace and structural applications.
Sendzimir Mill (Cluster Mill)
Sendzimir mills, also known as cluster mills, utilize small work rolls in a cluster arrangement to achieve high reductions on thin aluminum sheet products. These aluminum rolling mills are capable of producing high-quality, uniform aluminum products with precise thickness control, making them suitable for applications like automotive body panels and electronic components.
Foil Rolling Mill
Foil rolling mills are specialized mills designed for producing aluminum foil. These mills are equipped with precise control systems to achieve the extremely thin gauges required for aluminum foil used in packaging, insulation, and other applications.