Aluminum is a versatile metal with a range of applications across industries, from aerospace to construction. One crucial property of aluminum that significantly influences its usability is its melting point. Understanding the melting point of aluminum and its effects is vital for various processes and applications.
What Is The Melting Point Of Aluminum?
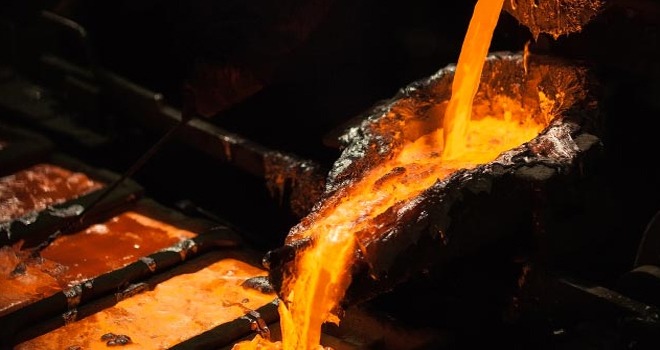
The melting point of a substance signifies the temperature at which it shifts from a solid to a liquid. Materials with higher melting points demand more energy for this transition, while those with lower melting points require less. This energy disparity allows some materials to liquefy at lower temperatures, whereas others stay solid until exposed to higher temperatures. Pure aluminum, in its elemental form, has a melting point of 1220.58°F (660.32°C). However, aluminum is predominantly utilized in alloy form rather than in its pure state. The composition of the alloy can substantially lower the melting temperature compared to pure aluminum.
What's The Melting Temperature Range Of Aluminum Alloy?
Aluminum alloy grades can be classified based on the manufacturing process, such as die-cast alloys and extruded alloys.
Die Cast Aluminum Alloy Melting Temperature
Die-cast aluminum is formed by injecting molten metal into a mold under high pressure, producing intricate shapes with accuracy. These aluminum alloys are classified into series according to their composition, such as the 1000 Series (pure aluminum), 2000 Series (high strength), 3000 Series (formability, corrosion resistance), 5000 Series (moderate to high strength), 6000 Series (heat treatable), and 7000 Series (high strength). Included below are the melting ranges for some prevalent alloys.
Aluminum | Melting Temperature |
1100 aluminum | 1190 – 1215°F |
2024 aluminum | 935 – 1180°F |
3003 aluminum | 1190 – 1210°F |
5052 aluminum | 1125 -1200°F |
5456 aluminum | 1055-1180°F |
6061 aluminum | 1080 – 1205°F |
7075 aluminum | 890 – 1175°F |
Alloying Elements' Impact on Melting Points in Aluminum Alloys
- Copper: Lowers the melting point. Alloys with more copper have lower melting points.
- Magnesium: Raises the melting point. Alloys with higher magnesium content exhibit higher melting points.
- Manganese: Variably influences melting points based on concentration.
- Silicon: Has a minor effect on melting points.
- Zinc: Can raise or lower melting points based on concentration and other elements present.
Extruded Aluminum Alloy Melting Temperature
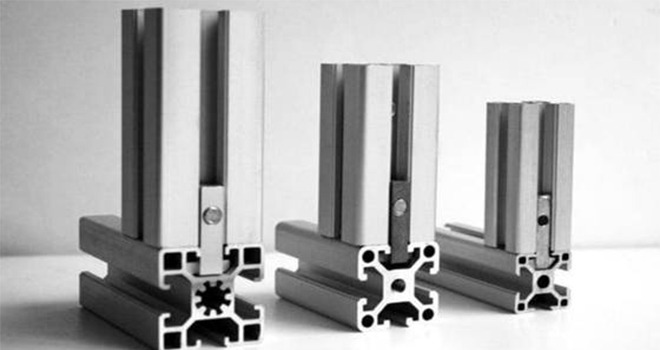
Extruded aluminum is shaped by forcing the metal through a die. Common extruded aluminum grades include A360, A380, A413, and B390. A360 offers good castability, A380 excels in fluidity, A413 provides strength and machinability, and B390 boasts high strength. These grades typically have melting temperatures ranging from 1100°F to 1300°F (590°C to 705°C), vital for casting and shaping processes in industries like automotive and construction.
Aluminum | Melting Temperature |
A360 | 1030 – 1100 °F |
A380 | 1000 – 1100 °F |
A413 | 1070 – 1080 °F |
B390 | 950 – 1200 °F |
Factors Influencing Aluminum Melting Point
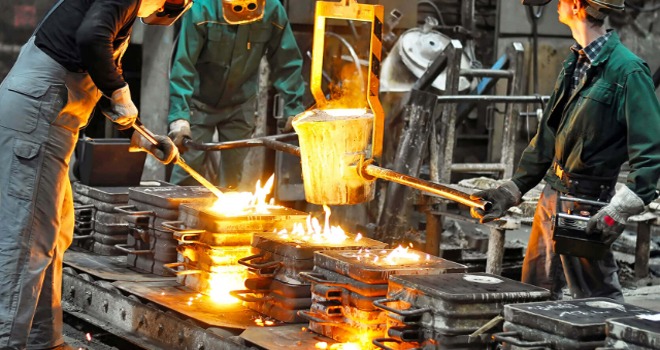
Aluminum’s melting point is influenced by a range of critical factors, encompassing chemical impurities, molecular composition, force of attraction, and pressure effects.
Chemical Impurities
Chemical impurities in aluminum alloys induce a melting point depression unintentionally. An alteration exceeding 41°F signals the presence of impurities. Sources of impurities include infiltration during melting, casting, and secondary production, impacting the alloy’s melting properties.
Molecular Composition
Influenced by aluminum’s covalent bonds, a significant amount of energy is needed to break them, leading to its elevated melting point in contrast to metals with weaker bonds.
Force of Attraction
The robust polar bonds present in aluminum lead to reduced volatility, elevated melting and boiling points, and a compact molecular arrangement, highlighting their importance.
Pressure Effects
The application of pressure, like approximately 3,500 gigapascals, can trigger re-entrant heating in aluminum, resulting in a reduction of the melting point above a specific critical pressure level.
Influence of Aluminum Melting Points on Industry Applications
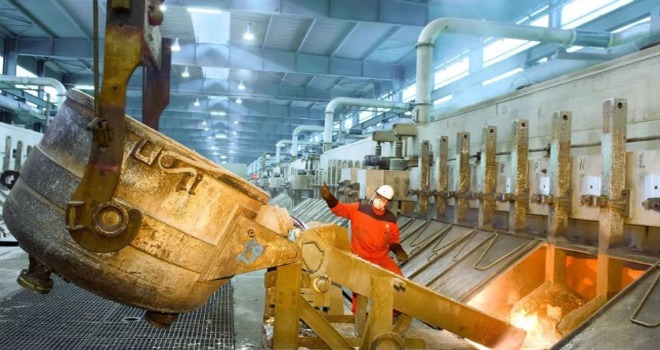
The melting point of aluminum is a critical factor that significantly influences its applications across various industries. Different aluminum grades with specific melting points are strategically chosen to cater to the unique requirements of each sector.
Aluminum In aerospace industry
In the aerospace industry, aluminum grades like 2024 or 7075 are preferred due to their high melting points, which enable them to withstand elevated temperatures. This makes them ideal for critical components such as aircraft frames, skins, and engine parts where durability under extreme conditions is essential.
Automotive Aluminum
Automotive manufacturing relies on aluminum alloys like A380 or A360, which have moderate melting points. This characteristic facilitates die-casting processes required for producing body frames, engine components, and wheels with precision and efficiency.
Aluminum For Construction
Within the construction sector, aluminum grades such as 6061 or 6063, known for their high melting points, are utilized for structural elements like beams, columns, and architectural facades. The elevated melting temperature of these alloys ensures the structural integrity and longevity of constructions in various architectural projects.
Electronics Aluminum
In the realm of electronics and electrical engineering, aluminum grades with moderate melting points like 1100 or 6061 are favored for their thermal management properties. These alloys are often employed in the production of heat sinks, electrical enclosures, and wiring components, where efficient heat dissipation is crucial.
Aluminum For Packaging
The packaging industry benefits from aluminum grades with lower melting points such as 3003 or 8011. These alloys are easily formable and are commonly used in the manufacturing of foil packaging, cans, and containers due to their malleability at relatively lower temperatures.
Marine Grade Aluminum
For marine applications that demand corrosion resistance, aluminum grades like 5083 or 6061 with high melting points are preferred. These alloys are employed in the construction of ship hulls, masts, and marine components, providing durability and longevity in harsh marine environments.