As the demand for NEV continues to rise, the manufacturing process of electric motor housing is evolving to incorporate advanced technologies such as additive manufacturing and automation. These innovations not only streamline production but also enable the creation of highly customized and optimized housings for different vehicle models.
What Is NEV
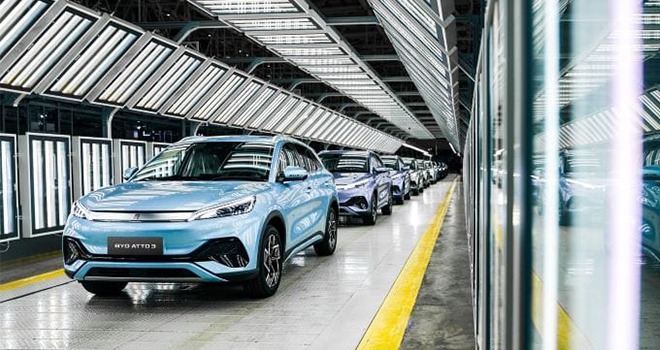
NEV stands for “New Energy Vehicle,” a category that includes vehicles powered by alternative energy sources such as electric vehicles (EVs), hybrid electric vehicles (HEVs), plug-in hybrid electric vehicles (PHEVs), and hydrogen fuel cell vehicles. These vehicles aim to reduce reliance on traditional fossil fuels, offering environmentally friendly transportation solutions with lower emissions and higher energy efficiency.
NEVs Types
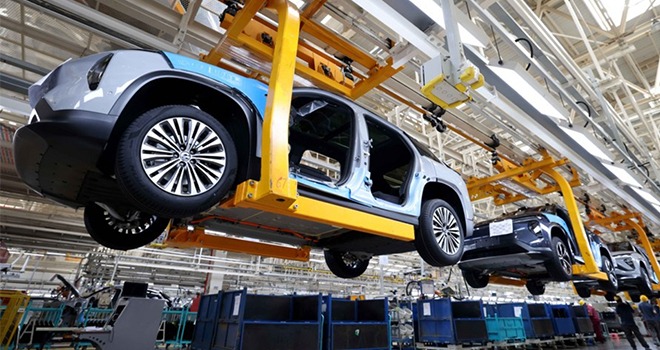
Electric Vehicles (EVs)
Electric vehicles are powered solely by electricity stored in batteries. They produce zero tailpipe emissions, offering a clean and efficient mode of transportation. EVs are charged by plugging into an electrical power source, and they are becoming increasingly popular as advancements in battery technology extend their range and reduce charging times.
Hybrid Electric Vehicles (HEVs)
Hybrid electric vehicles combine an internal combustion engine with an electric drive motor and a battery. They can run on gasoline, electricity, or a combination of both. HEVs are designed to improve fuel efficiency and reduce emissions by utilizing the electric drive motor during low-speed driving and the combustion engine at higher speeds.
Plug-in Hybrid Electric Vehicles (PHEVs)
Plug-in hybrid electric vehicles are similar to HEVs but with a larger battery that can be charged by plugging into an external power source. This allows PHEVs to travel longer distances on electric power alone before the internal combustion engine is engaged. PHEVs offer the flexibility of running on electricity for shorter commutes and switching to gasoline for longer trips.
Hydrogen Fuel Cell Vehicles
Hydrogen fuel cell vehicles use hydrogen gas to generate electricity through a chemical reaction with oxygen in the fuel cell stack. This electricity powers an electric drive motor, producing only water vapor as a byproduct. Hydrogen fuel cell vehicles offer fast refueling times and long driving ranges, making them a promising zero-emission alternative to traditional gasoline-powered vehicles.
Why Use Aluminum For NEV's Motor Housing
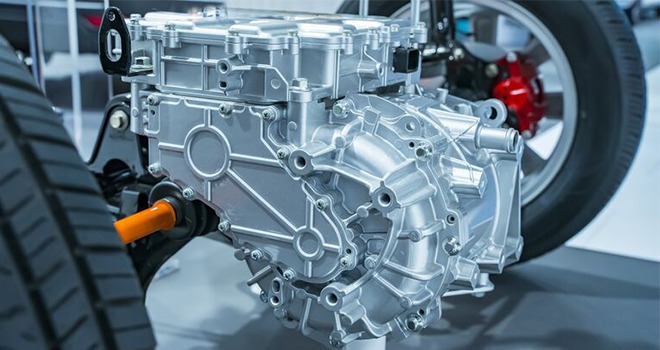
Aluminum housing is commonly used for the electric motor in New Energy Vehicles (NEVs) due to several key features that align well with the requirements of these vehicles:
Electromagnetic Shielding
Aluminum housing has excellent electromagnetic shielding properties, which are crucial in NEVs to minimize electromagnetic interference and ensure the smooth operation of sensitive electronic components in the electric motor system.
Noise Reduction
Aluminum’s natural damping properties help reduce vibrations and noise generated by the electric motor, contributing to a quieter driving experience in NEVs and enhancing overall comfort for passengers.
Thermal Expansion Matching
Aluminum’s thermal expansion coefficient closely matches that of certain components within the electric motor system, reducing the risk of mechanical stress and ensuring the structural integrity of the housing under varying temperatures and operating conditions.
Integration with Cooling Systems
Aluminum housing’s compatibility with various cooling technologies, such as liquid cooling systems or heat sinks, makes it an ideal choice for electric motor housings in NEVs, enabling efficient heat dissipation and thermal management to optimize performance and longevity.
Manufacturing Process Of The Aluminum Housing

The manufacturing process characteristics of the electric motor housing for new energy vehicles mainly manifest in the following aspects:
First - Material Selection
Aluminum Alloy Material: The electric motor housing of new energy vehicles commonly uses aluminum alloy as the primary material, such as ADC12 aluminum. ADC12 is a specific grade of aluminum alloy. In the aluminum alloy designation system, the prefix “A” indicates that it is an aluminum alloy, and the “DC” in ADC12 aluminum stands for “die casting”. The number “12” in ADC12 aluminum represents the specific alloy within the ADC series.
Next - Manufacturing Process
Die Casting Process
The motor casing can be designed in a two-piece design and produced through die-casting. This production method requires special attention to the quality of the sealing surface to ensure the sealing performance of the components.
The design of the integrated motor casing is also continuously evolving. In order to meet the production requirements of this design, processes such as low-pressure die casting and CPS sand core casting are considered for production.
Sand Casting
The shape of internal sand cores is achieved using methods such as hot core boxes or cold core boxes, with the hot core box method commonly used in mass production processes.
During the casting process, the casting is filled and solidified from the bottom up under a certain pressure to reduce the generation of trapped air, eddies, and other phenomena, which is beneficial for venting and reducing casting defects.
High-pressure Die Casting
Pressure die casting is a method where liquid or semi-solid metal fills the casting cavity at a high speed under the pressure of a piston and solidifies under pressure to obtain the casting.
Considerations In Manufacturing Process
Structural Features
- Cooling Channels: Motor housings require cooling channels to meet heat dissipation requirements, necessitating complex internal structures and high manufacturing precision.
- High Sealing Requirements: Internal sealing of the motor housing is crucial to prevent coolant leakage, leading to very high quality requirements for sealing surfaces.
Machining Precision
- Large Diameter Precision Machining: The diameter of the main hole in the motor housing depends on the size of the stator. High-precision machining techniques are needed for large main hole diameters to meet the requirements of high energy density for electric vehicles.
- Thin Walls Prone to Deformation: To increase power density, motor housings need to be light and small, requiring precise control of wall thickness to prevent deformation.
High Tech In Manufacturing Process
- 3D Printing Technology: Some high-end new energy vehicle motor housings utilize 3D printing technology for rapid manufacturing of complex structures. For example, Porsche introduced the first electric motor housing completely manufactured using 3D printing and additive manufacturing technology.