Corrosion resistance is a crucial property for aluminium, particularly in environments where it is exposed to moisture and other corrosive elements. This blog delves into effective strategies and maintenance practices to enhance the corrosion resistance of aluminium, ensuring its longevity and durability.
Will Aluminum Rust?
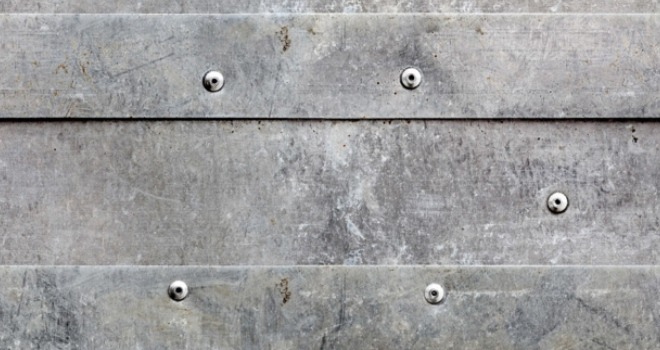
Aluminum does not rust in the same way that iron and steel do because it does not contain iron. Rust is a specific form of corrosion that occurs when iron or iron alloys are exposed to oxygen and moisture, leading to the formation of iron oxide (rust).
Aluminum, on the other hand, forms a thin layer of aluminum oxide on its surface when exposed to oxygen, which acts as a protective barrier against further corrosion. This oxide layer helps prevent aluminum from rusting but can still undergo corrosion under certain conditions.
While aluminum does not rust like iron, it can corrode over time, particularly in acidic or salty environments. This corrosion is typically referred to as oxidation rather than rusting. Proper maintenance and protective measures can help mitigate corrosion and ensure the longevity of aluminum structures and products.
Types Of Aluminum Corrosion
The types of corrosion in aluminum can be broadly categorized into general corrosion and localized corrosion. General corrosion affects a large area uniformly, while localized corrosion is more aggressive in concentrated areas. Both categories can be subdivided into various forms of corrosion that are influenced by factors like temperature, electrolyte chemistry, and the presence of other metals. Aluminum corrosion may include:
General Corrosion: This type of corrosion affects a large area of the aluminum surface uniformly, causing gradual degradation over the entire surface. In moist environments, such as those with high humidity or exposure to moisture, general corrosion on aluminum surfaces can be accelerated. Similarly, acidic environments, whether in the atmosphere or industrial settings, can induce general corrosion on aluminum.
Localized Corrosion:
- Pitting Corrosion: Small pits or craters form on the metal surface, often due to localized chemical reactions. Pitting corrosion can occur in environments with chloride ions, such as marine environments or areas exposed to salt spray.
- Crevice Corrosion: Occurs in confined spaces or crevices where the electrolyte is stagnant, leading to accelerated corrosion.
- Filiform Corrosion: Thin, thread-like filaments of corrosion that spread beneath the paint or protective coating.
- Galvanic Corrosion: When two dissimilar metals are in contact in the presence of an electrolyte, leading to accelerated corrosion of the less noble metal (aluminum in this case).
How to Enhance Aluminium Corrosion Resistance?
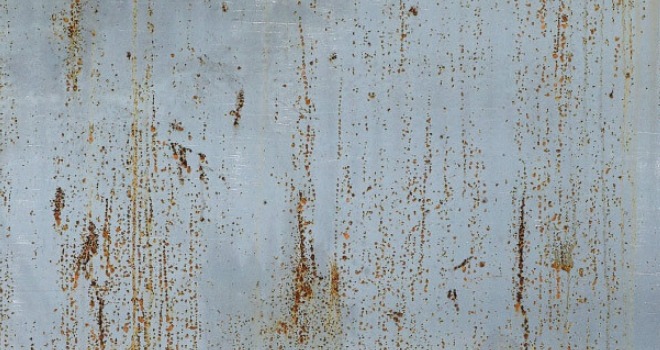
To fortify aluminium against specific types of corrosion, tailored methods can be employed:
Principle of Enhancing Aluminum Corrosion Resistance
Enhancing the corrosion resistance of aluminum involves implementing protective measures to create barriers on its surface. These barriers shield the aluminum from corrosive elements in the environment, such as moisture, salts, acids, or other metals, thereby increasing its durability and longevity. By fortifying the surface with these protective measures, aluminum becomes more resistant to corrosion, maintaining its structural integrity over an extended period.
Aluminium Corrosion Resistant Methods
Avoiding aluminum corrosion include methods such as anodizing, alodining, painting, or powder coating.
Anodizing Corrosion Resistant Aluminium
Anodizing stands out as a potent method for thwarting general corrosion in aluminium. This technique involves submerging the metal in an electrolytic bath, thereby bolstering the natural oxide layer and fortifying protection against environmental elements. Notably effective in damp surroundings and against atmospheric acids, anodizing serves as a reliable shield for the metal.
Furthermore, anodizing offers more than just corrosion resistance. It opens the door to color dyeing options, enhancing not only protective qualities but also bestowing a touch of aesthetic allure to the corrosion resistant aluminium surface.
Alodining Corrosion Resistant Aluminium
Alodining, known for its prowess as a conversion coating method, emerges as a potent solution against general corrosion and localized forms like crevice corrosion in aluminium. Although not as robust as anodizing, this technique creates a thin protective film that acts as a primer, effectively safeguarding the metal from moisture exposure and acidic conditions.
Moreover, Alodining offers more than just corrosion resistance. It serves as an ideal base for subsequent painting processes, providing a dual-layered shield against corrosion, ensuring the longevity and durability of the corrosion resistant aluminium components.
Painting Aluminum
The high electrical resistance inherent in the liquid paint acts as a protective shield, effectively separating the aluminum from direct contact with other metals. This insulation is pivotal in halting the electrochemical reactions that trigger galvanic corrosion.
In environments where dissimilar metal combinations coexist, galvanic corrosion is a prevalent risk due to the differing electrochemical potentials of the metals. By encasing the aluminum in a layer of high resistance paint, the likelihood of galvanic corrosion between these metal variants is significantly mitigated.
By deploying high electrical resistance liquid paint on aluminum surfaces, the metal is shielded from the corrosive effects of galvanic reactions, particularly in settings with mixed metal compositions, ensuring prolonged durability and protection.
Powder Coating Aluminum
Powder coating stands as a formidable defense against corrosion types like galvanic corrosion, offering protection against pitting and crevice corrosion. By adhering closely to the corrosion resistant aluminium surface, it minimizes the chances of peeling and chipping, rendering it ideal for challenging environments.
Moreover, powder coating presents a myriad of coloring options and boasts eco-friendliness compared to traditional liquid painting techniques. This makes it a robust and sustainable choice for safeguarding aluminum against corrosion, ensuring longevity and aesthetic appeal in equal measure.