In sheet, rod, and extrusion production, aluminum plays a vital role. How strong is aluminum, and what factors influence its robustness? Do different aluminum grades vary in strength? Exploring these aspects unveils the diverse capabilities of this versatile metal.
The Strength Of Aluminum
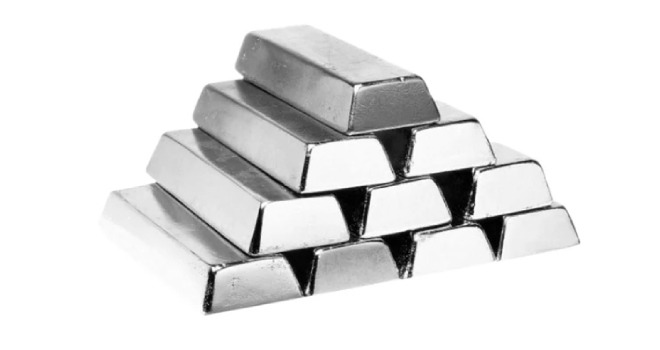
The strength of aluminum can demonstrate the robustness of this metal. By showcasing varying degrees of strength, aluminum proves to be a reliable and essential material in numerous applications.
How To Define Aluminum Strength?
Defining the strength of aluminum involves assessing its capacity to endure a specific load or stress before reaching defined levels of deformation or strain. This evaluation is often represented through stress-strain curves, generated by subjecting aluminum samples to tension until they rupture. Aluminum strength, typically measured in MPa or ksi, reflects the material’s ability to resist deformation, quantified as a percentage of the original sample length.
Two Important Points Of Aluminum Strength
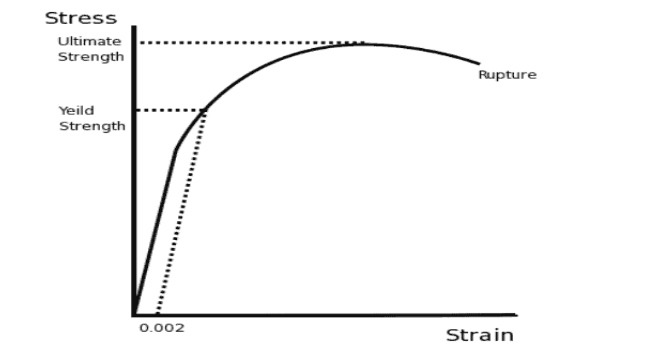
Two crucial aspects define aluminum strength: yield strength and ultimate strength.
Yield strength for aluminum denotes the maximum load aluminum can endure before exhibiting permanent deformation. Prior to this point, any deformation can be reversed upon load removal, akin to a stretched rubber band that rebounds to its original shape.
Conversely, aluminum ultimate strength represents the peak stress aluminum can withstand before failure or rupture, with all deformation post yield strength being irreversible plastic deformation.
The stress-strain assessment can employ various forces, with the prevalent method involving tensile strength application, essentially pulling the material apart. This test aids in determining the ultimate tensile strength, a key metric for comparing strength levels.
Comparing Aluminum Strength: Other Metals vs Aluminum
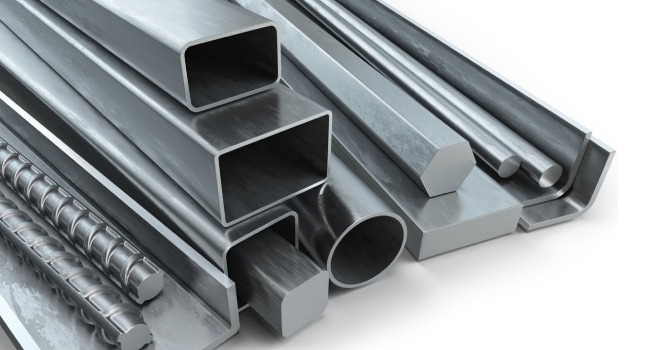
When comparing the strength of aluminum to other metals, the outcome depends on various factors such as the specific alloy, processing techniques, and intended application. Generally, aluminum offers a favorable strength-to-weight ratio, making it a preferred choice in industries where lightweight materials with decent strength properties are needed.
Aluminum vs. Steel
- Strength: Steel is generally stronger than aluminum.
- Aluminum vs Steel Weight: Aluminum is significantly lighter than steel.
- Applications: Steel is commonly used in structural applications where strength is paramount, while aluminum is favored in industries requiring lightweight properties such as aerospace and automotive.
Aluminum vs. Copper
- Strength: Copper is usually stronger than aluminum.
- Weight: Aluminum is lighter than copper.
- Applications: Copper is often utilized in electrical applications and plumbing due to its conductivity, while aluminum is preferred in areas where weight reduction is crucial.
Aluminum vs. Titanium
- Strength: Titanium is generally stronger than aluminum.
- Weight: Titanium is denser than aluminum but still lighter than steel.
- Applications: Titanium is commonly used in aerospace, military, and medical applications where a combination of strength and lightness is required. Aluminum is more widely used due to its cost-effectiveness and ease of fabrication in various industrial applications.
Aluminum vs. Brass
- Strength: Brass is generally stronger than aluminum.
- Weight: Aluminum is lighter than brass.
- Applications: Brass, known for its corrosion resistance and decorative properties, is commonly used in musical instruments, plumbing fittings, and decorative hardware. Aluminum, on the other hand, is preferred in lightweight applications such as aircraft construction and consumer electronics.
Why Aluminum's Lower Strength Doesn't Hinder Its Utility
Aluminum’s strength-to-weight ratio is a standout feature, outshining other metals like steel, copper, and titanium. Despite not being the strongest metal, aluminum’s lightweight nature coupled with its decent strength makes it a prime choice for weight-sensitive applications in aerospace, automotive, and marine industries. This unique advantage allows for optimal performance while minimizing the overall weight of structures and components, contributing to enhanced fuel efficiency and performance in various engineering applications.
What Is The Strongest Aluminum Alloys?
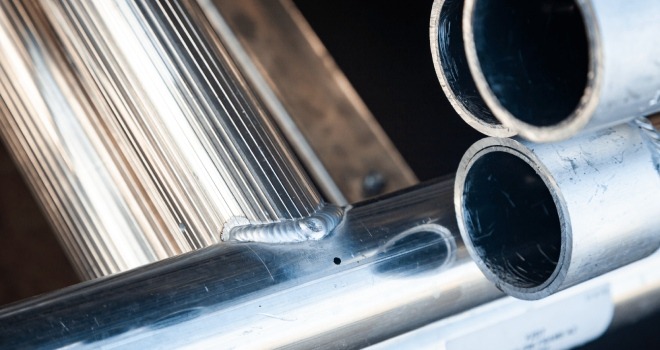
The ultimate tensile strength of aluminum is greatly variable due to the diverse grades available, each formulated with specific alloying elements in varying proportions that directly influence its strength. While pure aluminum is notably soft and weak, certain aluminum alloys can exhibit impressive levels of strength.
How Aluminum Grade Affects Aluminum Strength?
The aluminum strength is significantly influenced by the specific grade or alloy of aluminum being used. Here’s how a different aluminum grade can affect the strength of the material:
Alloying Element
The addition of an alloying element such as copper, zinc, magnesium, silicon, or manganese can enhance the strength of aluminum. Each alloying element contributes unique properties that impact the final strength of the aluminum alloy.
Heat Treatment
A different aluminum grade may undergo specific heat treatment processes to enhance its strength. Heat treatment methods like annealing, precipitation hardening, and quenching can modify the microstructure of the aluminum, improving its mechanical properties.
Processing Technique
The processing technique used during the manufacturing of aluminum components, such as rolling, extrusion, or forging, can also influence the strength of the final product.
Temper Designation
An aluminum grade is often assigned a temper designation (e.g., T6, T651) that indicates the specific heat treatment and mechanical properties of the material. This temper designation plays a crucial role in determining the strength and formability of the aluminum alloy.
The Strongest Aluminum Grade
Aluminum Grade | Ultimate Tensile Strength / Mpa |
2024 | 469 |
5052 | 228 |
6061 | 310 |
7075 | 572 |
The differences in ultimate tensile strength among various aluminum grades are primarily due to the specific alloying elements and heat treatment processes used in their formulation. Here’s a breakdown of why these differences exist:
-
2024 Aluminum: 2024 aluminum typically contains copper as the primary alloying element. The addition of copper enhances the strength of the aluminum, making it one of the stronger aluminum alloys commonly used in aerospace applications.
-
5052 Aluminum: 5052 aluminum is known for its excellent corrosion resistance and formability but has a lower ultimate tensile strength compared to 2024 aluminum and 7075 aluminum. Its strength is balanced with other properties to cater to specific applications where high strength is not the primary requirement.
-
6061 Aluminum: Alloy 6061 is a versatile grade with magnesium and silicon as its primary alloying elements. It offers good formability, weldability, and corrosion resistance while still providing moderate strength suitable for a wide range of applications.
-
7075 Aluminum: 7075 aluminum is one of the strongest aluminum alloys available, primarily due to the presence of zinc as a key alloying element. It is commonly used in applications where high strength-to-weight ratio is crucial, such as in aerospace and high-performance sports equipment.