Aluminum alloys are widely recognized for their versatility and exceptional properties that have revolutionized various industries. With a wide range of alloying elements and compositions, different types of aluminum alloys offer unique characteristics and benefits suited for specific applications.
In this blog, we will delve into the world of aluminum alloys, exploring various types, their uses, key features, and the benefits they bring to diverse industries. Specific properties and applications may vary depending on the exact alloy composition, and it is advisable to refer to the technical data of specific alloys and consult manufacturers (Aluminum Land) for information regarding the performance and suitability of a particular alloy in specific applications.
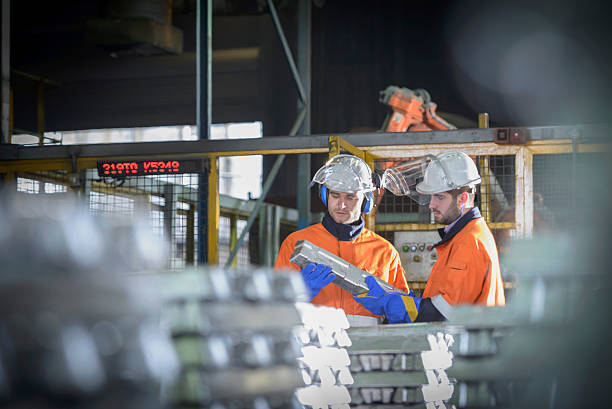
The Types of Aluminum Alloys
Aluminum alloys offer a wide range of options with diverse properties to meet different requirements. These alloys can be tailored to possess specific characteristics such as high strength, corrosion resistance, formability, weldability, and thermal conductivity. This versatility allows them to be utilized in a multitude of industries and applications, including aerospace, marine, automotive, construction, and more.
Alloy Series | Alloying Elements | Characteristics | Applications |
1xxx | Pure Aluminum | Excellent corrosion resistance, high thermal conductivity, good formability and electrical conductivity | Electrical wiring, cooking utensils |
2xxx | Copper | High strength, good machinability, poor corrosion resistance, heat treatable | Aerospace structural components |
3xxx | Manganese | Moderate strength, good formability, excellent corrosion resistance | Automotive parts, heat exchangers |
4xxx | Silicon | Low melting point, good fluidity in casting, susceptible to hot cracking | Welding filler wire |
5xxx | Magnesium | Good strength, excellent corrosion resistance, weldable | Boat hulls, architectural applications |
6xxx | Magnesium, Silicon | Good formability, moderate strength, heat treatable ![]() | Extrusions, automotive components |
7xxx | Zinc, Magnesium, Copper | Very high strength, heat treatable, poor corrosion resistance | Aerospace applications, high-stress structural parts |
8xxx | Other Elements (e.g., Lithium) | Specialized alloys with unique properties | Lithium-ion battery components |
1xxx Series Aluminum Alloys
The 1000 series aluminum alloys belong to the commercially pure aluminum group, consisting of aluminum as the primary alloying element.
- These alloys are characterized by their high purity, excellent corrosion resistance, and good electrical conductivity.
- They are non-heat treatable, meaning they do not gain significant strength through heat treatment processes.
The most common alloy in the 1xxx series is 1100 aluminum, which has a minimum aluminum content of 99.00%. It is known for its high formability, weldability, and resistance to corrosion. Due to its excellent electrical conductivity, 1100 alloy is frequently used in electrical conductors, transformer windings, and heat exchangers. The 1xxx series aluminum alloys are also highly ductile, making them suitable for applications that require deep drawing or spinning, such as kitchen utensils, signage, and reflectors. They are often chosen for their aesthetic appeal, as their high reflectivity allows for a bright and polished surface finish.
2xxx Series Aluminum Alloys
It is primarily alloyed with copper, and sometimes with small additions of other elements such as manganese or magnesium. The most common alloy in this series is 2024 aluminum, which is widely used in aerospace applications due to its exceptional strength-to-weight ratio.
- Alloys in the 2xxx series are heat treatable, meaning their mechanical properties can be further enhanced through precipitation hardening.
- It also offers good machinability and can be easily formed.
However, they may exhibit reduced corrosion resistance compared to other aluminum alloys. Therefore, proper surface protection or the use of protective coatings is often required when using these alloys in corrosive environments.
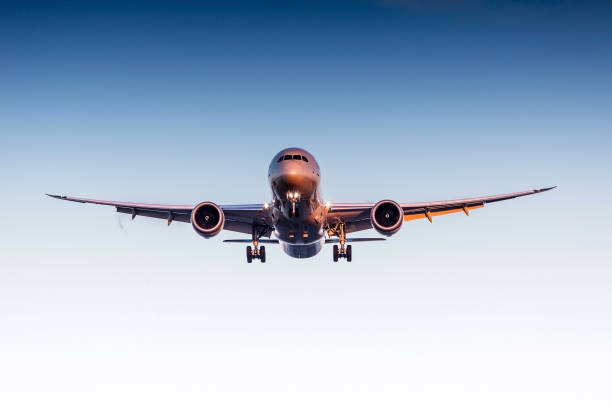
3xxx Series Aluminum Alloys
- The 3000 series alloys are non-heat treatable
However, they can be cold-worked to increase their strength and improve their mechanical properties. These alloys are alloyed primarily with manganese, with small additions of other elements such as copper or magnesium. The most common alloy in this series is 3003 aluminum, which is widely used in various applications. These alloys offer excellent corrosion resistance and good thermal conductivity, particularly in environments where exposure to moisture or chemicals is a concern. They are often used in applications such as cooking utensils, heat exchangers, and chemical equipment.
4xxx Series Aluminum Alloys
The 4xxx series aluminum alloys are a group of aluminum alloys primarily composed of aluminum and silicon.
- These alloys exhibit good formability, weldability, and corrosion resistance, making them commonly used as filler materials for welding aluminum components.
- They have higher melting points and lower heat treatability, typically used in the as-welded or as-cast condition.
These alloys find wide applications in industries such as automotive, construction, and general manufacturing, serving as filler materials for automotive parts, bicycle frames, and heat exchangers, as well as in casting applications for automotive engine components, electrical connectors, and decorative parts. While offering good corrosion resistance, the 4xxx series alloys are not as corrosion-resistant as other aluminum alloy series.
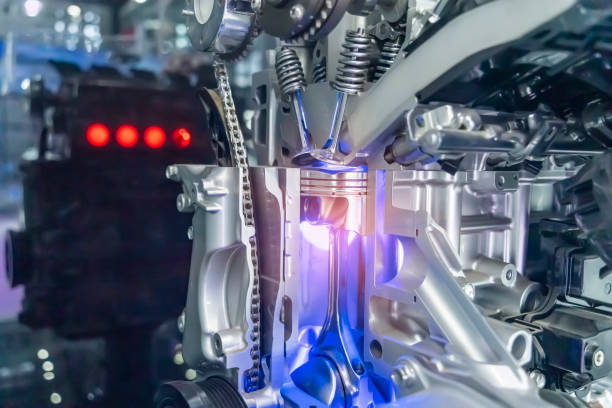
5xxx Series Aluminum Alloys
5xxx series aluminum alloys consist primarily of aluminum and magnesium as the major alloying elements. The most common alloy series is 5052 aluminum. With a higher magnesium content, they exhibit enhanced strength and hardness compared to other aluminum alloys. The 5xxx series alloys demonstrate excellent formability, allowing them to be easily shaped and formed using various manufacturing processes. Moreover, they offer exceptional corrosion resistance, particularly in marine and industrial environments, making them ideal for applications where protection against corrosion is vital. These alloys also possess good weldability, enabling them to be effectively joined using common welding techniques.
The 5xxx series aluminum alloys find extensive use across a wide range of industries, including transportation, marine, construction, and packaging. They are commonly employed in the production of automotive components, boat hulls, aircraft parts, architectural structures, etc.
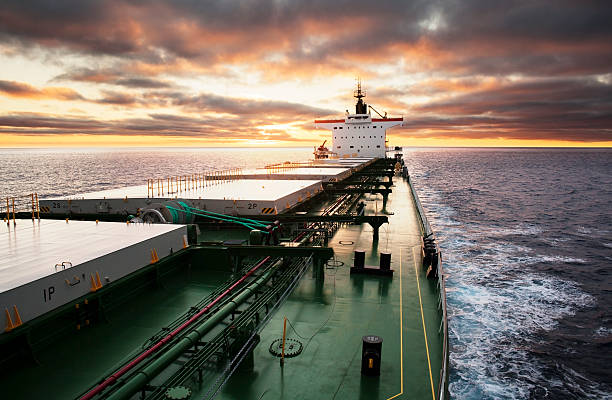
6xxx Series Aluminum Alloys
The 6000 series aluminum alloys are a group of alloys primarily composed of aluminum, magnesium, and silicon as the main alloying elements. It finds widespread use in industries such as automotive, aerospace, construction, and consumer goods. 6061 aluminum and 6063 are widely used in structural and architectural applications, as well as in the production of extruded profiles.
Alloying elements: The 6xxx series alloys contain magnesium and silicon in varying proportions. Magnesium provides strength and improves the alloy’s response to heat treatment, while silicon enhances its fluidity during casting.
Strength and formability: The 6xxx aluminum exhibit good strength and excellent formability.
Weldability: These alloys have good weldability, allowing for efficient joining using various welding techniques.
Corrosion resistance: While the 6000 series alloys offer moderate corrosion resistance, they are not as corrosion-resistant as some other aluminum alloy series. However, they can be enhanced with surface treatments or coatings to improve their resistance to corrosion in specific environments.
7xxx Series Aluminum Alloys
7000 Aluminum(7075 aluminum) primarily consists of aluminum, zinc, and magnesium as the major alloying elements. Copper is also commonly present in smaller amounts. They exhibit excellent mechanical properties, including tensile strength and fatigue resistance.
- Heat treatable
- Moderate corrosion resistance
Due to their exceptional strength, 7000 series aluminum is extensively used in aerospace applications and automotive industry. They are commonly employed in the manufacturing of aircraft structural components, such as wing spars, fuselage frames, and landing gear parts.
8xxx Series Aluminum Alloys
8000 aluminum alloys primarily consist of aluminum and typically contain elements such as lithium, tin, and occasionally copper.
- Heat treatable
- Lithium content: he significant addition of lithium in these alloys contributes to their enhanced strength and stiffness. The presence of lithium helps to improve their mechanical properties, including fatigue resistance and overall performance.
Lightweight and high strength: The 8xxx series alloys are known for their excellent strength-to-weight ratio. They offer exceptional strength while being lightweight, making them ideal for applications where weight reduction is crucial, such as in the aerospace industry.
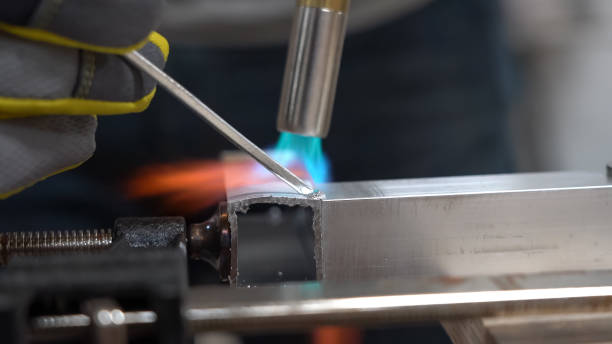
Benefits of Aluminum Alloys
Aluminum alloys offer significant advantages, including lightweight, strength, corrosion resistance, thermal conductivity, and recyclability. Their lightweight nature provides an advantage in terms of weight savings and energy efficiency. The combination of strength and corrosion resistance makes them suitable for applications that require high strength and durability. Aluminum alloys also exhibit excellent thermal conductivity and electrical conductivity, making them useful in thermal management and electrical fields. Moreover, the recyclability of aluminum alloys makes them an environmentally sustainable choice.