Aluminum is a versatile material known for its durability, light weight, and corrosion resistance. While it is commonly associated with various industrial applications, it is also a popular choice for consumer products and even artistic endeavors. One question that often arises is whether aluminum can be powder coated. The short answer is yes, aluminum can indeed be powder coated, and the process offers numerous benefits.
What Is Powder Coating?
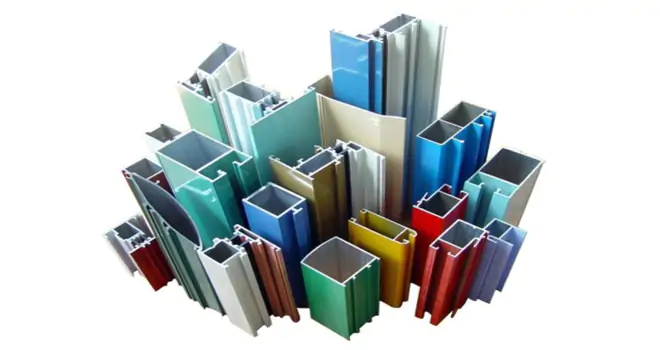
Powder coating is a dry finishing process where finely ground particles of pigment and resin are electrostatically charged and sprayed onto a metal surface. The charged particles adhere to the surface until heated and fused into a smooth coating in a curing oven. This results in a durable, high-quality finish that is resistant to chipping, scratching, fading, and wear.
Advantages Of Powder Coating
Advantages of using powder coating over traditional painting methods include:
Durability: Powder coating provides a more durable finish that is resistant to chipping, scratching, fading, and wear.
Environmentally Friendly: Powder coating is solvent-free and emits minimal VOCs, making it an eco-friendly option.
Efficiency: It is an efficient process with minimal waste, as unused powder can be collected and reused.
Variety: Powder coating offers a wide range of colors and finishes for customization.
Uniform Finish: Provides a smooth and even finish without drips, sags, or brush marks.
Disadvantages Of Powder Coating
Despite its many advantages, powder coating also presents several drawbacks that designers should take into consideration:
Challenging Touch-Ups: Repairing minor damages is difficult once powder coating has cured, often requiring recoating of the entire surface.
High Initial Costs: The equipment and setup costs for powder coating can be substantial, making it less cost-effective for small-scale or one-off projects.
Inconsistent Thickness: Achieving uniform thin coatings can be challenging with powder coating, potentially leading to fit or assembly issues.
Susceptibility to Fading: Without certain additives, powder-coated surfaces can fade over time due to exposure to sunlight, although this is generally less of an issue compared to liquid paint.
Difficulty in Coating Complex Parts: Coating complex parts evenly can be tough with powder coating, especially those with hidden interior surfaces, as it is typically applied using a spray gun.
Why Does Aluminum Need Powder Coating?
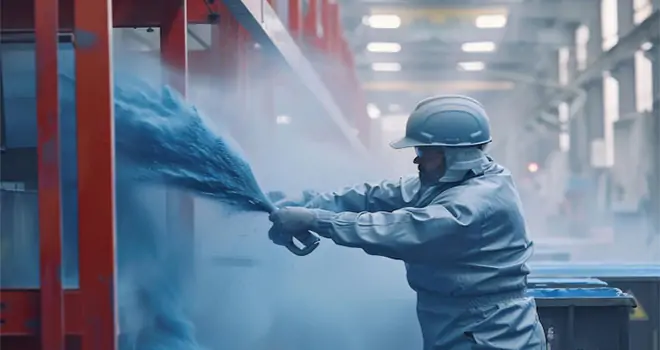
Aluminum necessitates powder coating across diverse applications for several compelling reasons. In architectural settings, powder coating shields aluminum structures from harsh weather elements, ensuring longevity and preserving aesthetics. It provides a durable finish that resists corrosion, scratches, and fading, maintaining the appearance of buildings for extended periods.
In automotive applications, powder coating on aluminum parts offers protection against road debris, chemicals, and UV exposure, enhancing both the visual appeal and structural integrity of vehicles. This coating method ensures that components retain their finish and functionality over time, contributing to the overall durability of the vehicle.
Within the industrial sector, aluminum equipment and machinery benefit significantly from powder coating. The protective layer adds a robust shield against abrasion, chemicals, and impacts, prolonging the lifespan of these essential components and reducing maintenance costs.
For consumer products like furniture, appliances, and outdoor equipment, powder coating on aluminum surfaces provides a vibrant and long-lasting finish that is resistant to scratches and wear. This application not only enhances the appearance of the products but also ensures they withstand daily use and exposure to various environments, making them more durable and appealing to consumers.
Different Types Of Powder Coat Aluminum
Various types of powder coatings are available for aluminum surfaces, each offering unique characteristics and benefits. Some common types include:
Epoxy Powder Coatings: Known for their excellent adhesion and chemical resistance, epoxy coatings are often used for indoor applications.
Polyester Powder Coatings: Polyester powder coat aluminum provides good weatherability and color retention, making them suitable for outdoor applications.
Epoxy-Polyester Hybrid Powder Coatings: Combining the properties of both epoxy and polyester, hybrid coatings offer a balance of durability and aesthetics.
Acrylic Powder Coatings: Acrylic powder coat aluminum provides UV resistance and are often used for automotive and architectural applications.
Polyurethane Powder Coatings: Offering exceptional durability and scratch resistance, polyurethane coatings are ideal for high-traffic areas.
Thermoplastic Powder Coatings: These coatings can be reheated and reshaped after curing, making them suitable for applications requiring post-coating forming.
How to Powder Coat Aluminum?
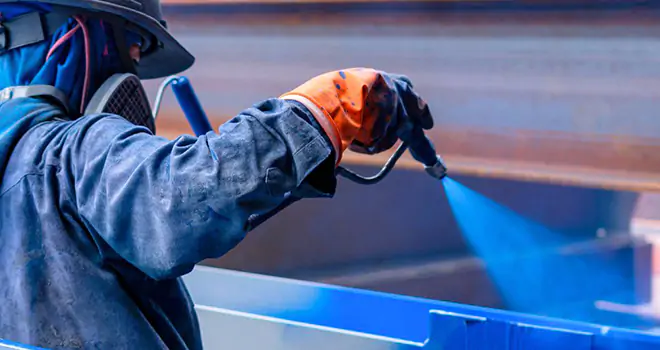
To powder coat aluminum effectively, a meticulous process must be followed to ensure a durable and high-quality finish. Here’s a detailed description of the steps involved in powder coating aluminum:
Step 1: Surface Preparation
Surface preparation is a critical initial step in the powder coating process. Before applying the powder, it is essential to clean the aluminum surface thoroughly. This involves removing any old coatings, debris, oil, or grime that may hinder adhesion. Techniques such as scraping, grinding, using solvents, pressurized water, and sandblasting are employed to achieve a clean and slightly rough surface texture, ideal for powder adhesion.
Step2: Powder Application
Once the surface is properly prepared, the powder application process begins. Coating specialists mix the powder formulation with color pigments, resins, and additives according to the desired specifications. Using an electrostatic spray gun, the powder coating is evenly applied to the aluminum surface. The positively charged powder particles adhere to the grounded aluminum part, ensuring a uniform coating. Any excess powder can be collected for reuse.
Step3: Curing
After the powder coating is applied, the aluminum parts need to undergo a curing process to ensure adhesion and durability. The coated parts are baked in an oven at temperatures typically not exceeding 390°F (200°C) for around 10-15 minutes. The exact time and temperature depend on the coating formulation, part size, and thickness. Curing allows the powder coating to melt, flow, and form a durable finish on the aluminum surface.
Step 4: Quality Inspections
Following the curing process, quality inspections play a crucial role in ensuring the integrity of the powder-coated aluminum parts. Inspectors evaluate the thickness, uniformity, and adhesion of the coating. Various inspection techniques, such as destructive testing and visual checks, may be employed to assess the quality of the powder coating. This step is essential for identifying and rectifying any defects or inconsistencies in the coating, ensuring a flawless final product.