When it comes to finishing aluminum surfaces, two popular methods stand out: anodizing and powder coating. Each technique offers unique advantages and considerations, making the choice between them a crucial decision for various applications. Let’s delve into the specifics of anodized and powder-coated finishes to determine which is better suited for aluminum.
Benefits Of Aluminum Powder Coating
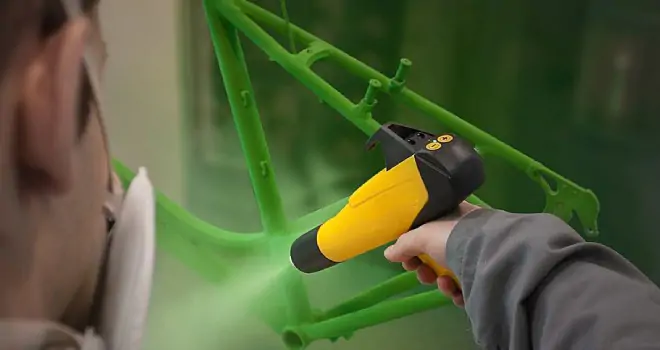
Aluminum powder coating provides a multitude of benefits, from exceptional corrosion resistance to versatile aesthetics.
Corrosion Resistance
Powder-coated aluminum stands strong against corrosion, creating a protective shield that shields it from moisture and corrosive elements, making it a prime choice for outdoor and high-humidity settings.
Versatility
Through the aluminum powder coating process, a vast spectrum of color options, finishes, and textures become available, allowing for extensive customization to suit diverse aesthetic preferences and applications.
Aesthetic Appeal
Powder-coated aluminum offers a polished and seamless finish, adhering uniformly to surfaces, enhancing the visual allure of structures, automotive components, and furniture.
Environmental Friendliness
Embracing eco-friendliness, powder coating for aluminum is free from harmful solvents and VOCs, with minimal waste production and the ability to recycle overspray, thereby reducing its environmental footprint.
Durability and Maintenance
Powder-coated aluminum boasts remarkable durability, resisting scratches, fading, and chemical damage, requiring minimal upkeep even in high-traffic areas, thus saving both time and expenses.
Cost-effectiveness
The efficient application process of aluminum powder coating cuts down on labor costs, while the enduring durability of the finish demands less frequent recoating or replacement, resulting in long-term financial benefits.
What Are The Benefits Of Anodized Aluminum?
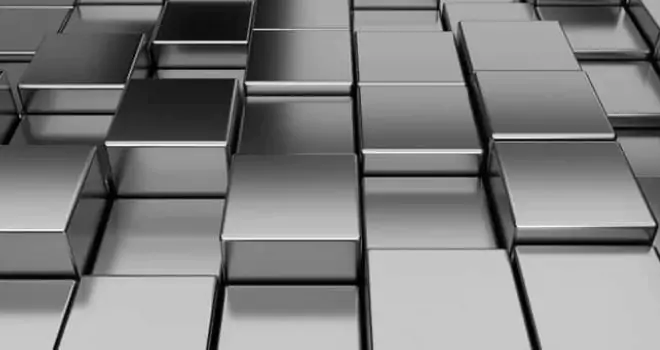
Anodized aluminum‘s benefits include improved corrosion resistance, superior lubrication properties, dyeing capabilities for color customization, and increased adhesion, making it a versatile and durable choice for various applications.
Corrosion Resistance
Anodized aluminum exhibits superior corrosion resistance compared to standard aluminum due to its thicker oxide layer, making it less susceptible to corrosion from moisture, air, salt, or other elements.
Lubrication
Anodizing aluminum offers improved lubrication capabilities over standard aluminum. The deeper pores created during the anodizing process enable better retention of lubricating oil or film, a feature lacking in standard aluminum with its smooth surface.
Dyeing
Anodized aluminum can be dyed to create vibrant products, unlike standard aluminum which typically retains its natural chrome color. The anodizing process, involving exposure to acid chemicals, forms a porous surface that enhances dye retention, allowing for a wide range of color options.
Increased Adhesion
Anodizing aluminum provides enhanced adhesion for adhesives and primers due to its deeper pores compared to standard aluminum. These pores act as channels for liquids, promoting better adhesion when coatings or adhesives are applied.
Anodized vs Powder Coat: How To Compare?

When comparing anodizing and powder coating for aluminum surfaces, several factors come into play to help you make an informed decision:
Appearance Of Anodized Finish And Powder Coat Finish
- Anodized finish offers a metallic finish with a range of colors but limited to metallic hues.
- Powder coating provides a broader color palette and texture options, allowing for more customization.
Durability Of Anodized Finsh And Powder Coat Finish
- Anodizing provides excellent wear and corrosion resistance, making it ideal for applications where longevity is crucial.
- Powder coating offers good protection against environmental elements but may be more prone to wear and scratching compared to anodizing.
Cost
- Anodized finish is generally more expensive due to the precision process and durability it provides.
- Powder coating is often more cost-effective, making it a preferred choice for projects with budget constraints.
Applications
- Anodizing is commonly used in industries such as automotive, electronics, and architecture for its precision and durability.
- Powder coating is popular in applications like household appliances, automotive parts, and outdoor equipment due to its variety of colors and textures.
Anodized vs Powder Coat: Which Is Better?
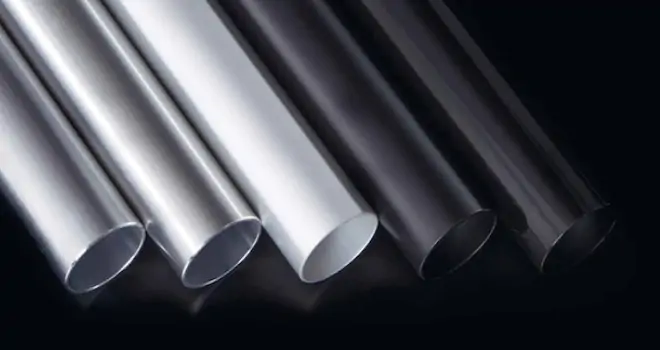
When faced with the decision between anodizing and powder coating for aluminum, precision and durability come to the forefront with anodizing. Anodized finish excels in maintaining tight dimensional tolerances, offering exceptional resistance to wear and corrosion, and presenting a sophisticated metallic sheen. Ideal for applications requiring meticulous engineering, such as in appliances, furniture, or automotive components, anodizing ensures lasting protection and a visually striking finish that embodies both strength and elegance.
On the other hand, powder coating emerges as a versatile solution emphasizing vibrant aesthetics and cost-effectiveness. With a wide spectrum of colors and textures that withstand the elements, powder coating is the go-to choice for applications demanding visual appeal without compromising on protection, like in household appliances, automotive parts, or playgrounds. It strikes a balance between aesthetics and durability, providing a customizable and enduring surface finish that caters to diverse design preferences and budget considerations.