When embarking on a new project, the choice of material can significantly influence its outcome. In the realm of metal selections, the decision between anodized aluminum and raw aluminum stands out as a critical one. Understanding the nuances between these two materials is key to making an informed choice that aligns with your project goals.
What Is Anodized Aluminum?
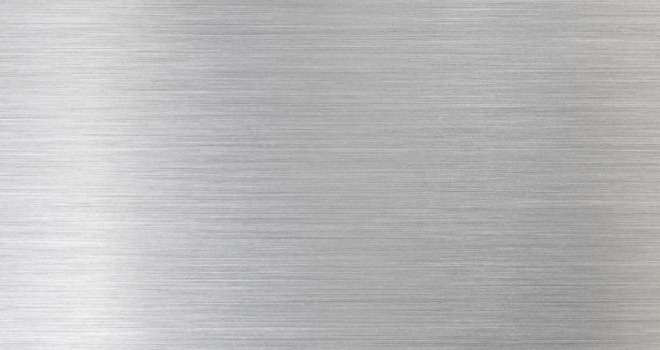
Anodized aluminum is a material that has been treated through a process known as anodization. This method involves amplifying the existing oxide layer on the surface of aluminum to improve its protective qualities. The oxide layer acts as a barrier against further oxidation and corrosion of the aluminum.
During the anodization process, aluminum is submerged in an electrolytic solution and exposed to an electric current. This procedure prompts oxygen ions to bind with the aluminum surface, resulting in a thicker and more robust oxide layer. Anodized aluminum is recognized for its heightened resistance to corrosion, wear, and abrasion in comparison to untreated aluminum.
Furthermore, anodized aluminum can be colored using various dyeing techniques, making it a favored option for architectural, automotive, and decorative purposes where both protection and visual appeal are crucial. The aluminum alloy anodizing process can yield a variety of finishes, ranging from matte to glossy, depending on the intended application.
Overall, anodized aluminum is esteemed for its improved durability, corrosion resistance, and decorative possibilities, rendering it a versatile material employed across a diverse array of industries.
Aluminum Alloy Anodizing Process
In the aluminum alloy anodizing process, technicians do not need to manually apply a substance to the aluminum surface, contrary to common belief. This method leverages the inherent reaction that naturally occurs on aluminum when exposed to specific elements, but it elevates this reaction to a more sophisticated level.
Once the aluminum has undergone a forming process, such as extrusion, the resulting aluminum alloy part is immersed in an electrolytic bath. Within this bath, a high-amperage, low-voltage electrical current is applied while the aluminum alloy is submerged. As the current flows through the aluminum alloy, a chemical reaction of oxidation takes place, resulting in the formation of an oxide layer that is thicker than the naturally occurring one.
The Advantages Of Anodized Aluminum
Anodized aluminum offers several advantages. It enhances wear resistance by forming a ceramic-like oxide layer that is more durable than untreated aluminum, making it resistant to scratches and nicks. Anodized aluminum’s porous surface allows for better adhesion of dyes, glues, and primers, resulting in a more uniform and strongly bonded finish. Additionally, anodized aluminum has superior heat dissipation capabilities due to its increased surface area, facilitating improved convective heat transfer and emissivity. Convective heat transfer, influenced by design and anodizing, aids in exchanging heat with the surrounding air, while anodizing significantly enhances radiative heat transfer between surfaces.
Anodized Aluminum vs Aluminum
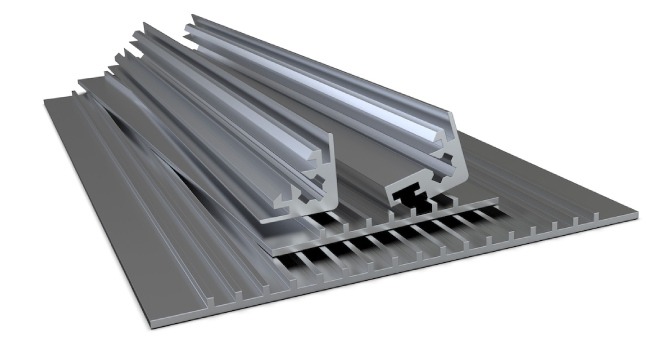
When comparing anodized aluminum to non-anodized aluminum across three key aspects—properties, applications, and cost—it becomes evident that these materials exhibit distinct characteristics in various contexts.
Anodized Aluminum vs Non Anodized Aluminum: Properties
Anodized Aluminum: Anodized aluminum is characterized by a robust oxide layer on its surface, significantly bolstering its resilience against wear, corrosion, and scratches. Moreover, the aluminum alloy anodizing anodizing procedure facilitates coloring and dyeing, presenting a spectrum of decorative choices.
Non-Anodized Aluminum: Conversely, non anodized aluminum lacks the protective oxide layer found in anodized aluminum. This deficiency makes it more vulnerable to corrosion and wear.
Anodized Aluminum vs Non Anodized Aluminum: Applications
Anodized aluminum and non-anodized aluminum offer distinct applications across various industries due to their unique properties and characteristics.
Anodized Aluminum Applications
Anodized aluminum, after undergoing electrochemical treatment to enhance its properties, is widely utilized across industries and products due to its improved resistance to corrosion, durability, and aesthetic appeal. This material finds various applications, including:
Commercial and Residential Building Products: Anodized aluminum is a popular choice for building materials due to its strength and ability to withstand environmental elements, thanks to its added corrosion resistance.
Furniture: The versatility of anodized aluminum in terms of colors, textures, and lusters makes it a preferred option in furniture manufacturing, especially where design aesthetics are crucial.
Sporting Goods: Anodized aluminum’s corrosion resistance makes it suitable for sporting goods, particularly for items exposed to water like boats, ensuring durability in challenging conditions.
Motor Vehicle Components: Apart from improving durability, anodized aluminum enhances the visual appeal of motor vehicle components, meeting the demands of consumer-facing automotive products.
Food Preparation Equipment: Anodized aluminum is essential in the food and beverage industry for its corrosion resistance, safeguarding against acidic and salty substances, thus prolonging the lifespan of equipment components.
Non Anodized Aluminum Applications
Non anodized aluminum, although lacking the protective oxide layer, remains a versatile material with diverse applications, such as:
Transportation: Lightweight and durable, non-anodized aluminum is a preferred choice in aircraft construction due to its impressive strength-to-weight ratio, also finding applications in ships, trains, and automobiles.
Electrical Components: The lightweight nature of non anodized aluminum makes it ideal for electrical components like power lines and consumer electronics, such as smartphones and tablets.
Consumer Products: Economical and easily mass-produced, non-anodized aluminum is commonly used in various consumer goods like televisions, window frames, and laptops.
Household or Industrial Appliances: The strength and corrosion resistance of aluminum make it suitable for precision tubing and cooling components in appliances like refrigerators, dishwashers, and air conditioners.
Anodized Aluminum vs Aluminum : Cost
Anodized Aluminum: The anodizing process adds to the cost of aluminum due to the additional steps involved in creating the oxide layer. However, the increased durability and aesthetic options may justify the higher cost for certain applications.
Non-Anodized Aluminum: Non anodized aluminum is generally more cost-effective compared to anodized aluminum since it does not undergo the additional processes required for anodization.