In the realm of aluminum stress relief, preserving structural integrity is paramount. Temperature and temper treatment stand as pivotal considerations in this process. These factors play a crucial role in alleviating internal stresses within the material, ensuring its longevity and performance. By meticulously controlling temperature variations and temper adjustments, manufacturers can optimize the mechanical properties of aluminum components, guaranteeing their durability and reliability in diverse applications.
What Is Aluminum Stress Relief?
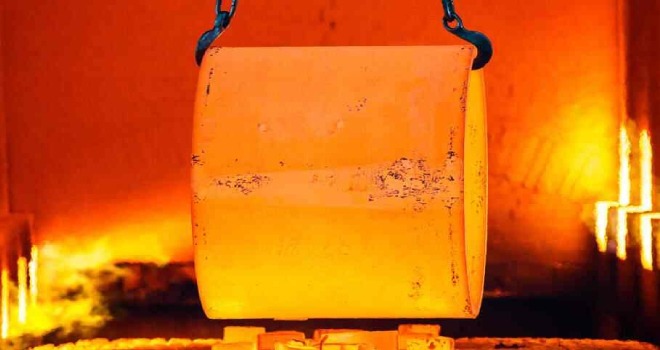
Aluminum stress relief is a vital process in mechanics that deals with internal forces within the material, termed stress, which can result in deformations. Strain, representing the deformity caused by this stress, reflects the internal pressure within the material. While the stress is intrinsic, external factors like gravity or contact forces can exacerbate it, potentially leading to deformations.
Residual stress, a common type, remains post-manufacturing and can weaken the material, making it more susceptible to deformations and fatigue. Structural stress evaluates the material’s ability to withstand applied forces, while thermal stress arises from temperature changes, causing the metal to expand and contract. Managing these stresses is essential for optimizing the structural strength and performance of aluminum components.
Aluminum Stress Relief Temperature
Aluminum stress relief temperature range is 570°F to 770°F due to its ability to facilitate the controlled relaxation of internal stresses within the material without causing excessive softening.
At these temperatures, the aluminum undergoes a process where the atoms within the crystal lattice have enough thermal energy to rearrange and reach a more stable state, effectively reducing the built-up stress from previous manufacturing processes like forming or machining.
By heating the aluminum within this specific range for up to three hours, the material can undergo a gradual and uniform stress relief process. This helps prevent any abrupt changes in the metal’s structure, ensuring that it retains its mechanical properties while effectively resolving issues such as warping that may have occurred during earlier fabrication stages. Additionally, the aluminum stress relief temperature range is particularly suited for alloys commonly used in industries that require stress relief treatments, providing an optimal balance between stress relief effectiveness and material integrity.
Aluminum Stress Relieving Heat Treatment Methods
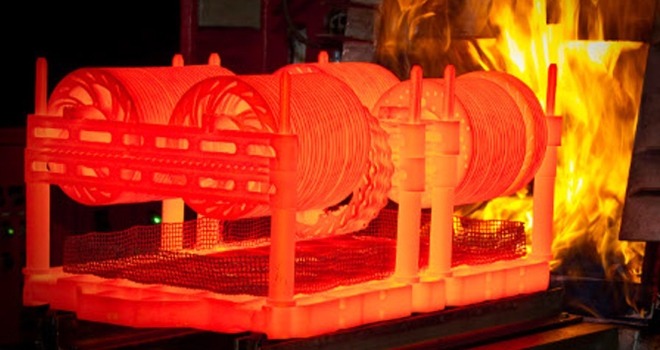
In the process of aluminum stress relieving heat treatments, various techniques are utilized to alleviate stress within the metal. Aluminum alloys commonly undergo work hardening early in their production cycle, deliberately deforming the material to alter its crystalline structure—a change that can be reversed through annealing.
During stress relief, aluminum undergoes heat treatment to rectify the altered crystalline structure resulting from work hardening. Annealing, a prevalent method, is employed to restore the metal’s properties, proving particularly useful for alloys that are typically non-heat treatable, like those found in the 3xxx, 4xxx, and 5xxx series.
Another method, known as solution heat treatment, involves rapidly cooling the metal after it reaches a specific temperature. This process preserves dissolved elements within the material, leading to an age hardening effect over time. While the metal is initially easy to work with post-quenching, it gradually hardens, impacting its temper and workability characteristics.
Aluminum Stress Relieving Heat Treatment Temper
In the domain of aluminum stress relieving heat treatments, a frequently utilized temper is T5. The T5 temper involves heating the aluminum alloy to a specific temperature range and subsequently quenching it to achieve a stable state. This procedure enhances the material’s strength and hardness, rendering it suitable for diverse applications.
The selection of the T5 temper in aluminum stress relieving heat treatment process is pivotal for augmenting the material’s characteristics. Through the T5 tempering process, the aluminum alloy acquires heightened strength and resistance to deformation, enhancing its durability and reliability in structural applications. Moreover, the T5 temper plays a crucial role in mitigating internal stresses within the material, ensuring its stability and optimal performance under varying conditions.
Aluminum Vibratory Stress Relief
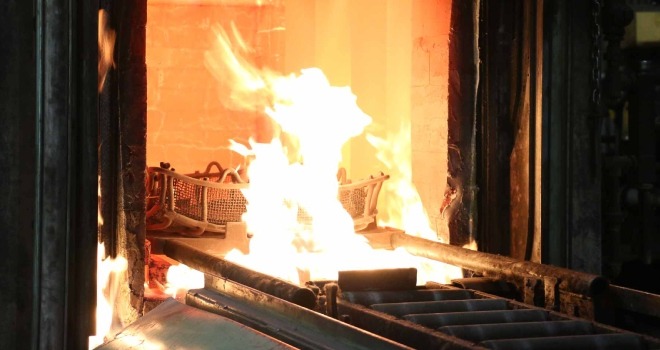
In addition to the commonly employed methods such as annealing, solution heat treatment, precipitation hardening, and stress relief annealing, vibratory stress relief stands as another effective technique that can alleviate internal stresses in aluminum, ultimately enhancing the material’s stability and performance.
Vibratory Stress Relief Advantages
Vibratory stress relief (VSR) stands out as a non-thermal technique employed in metalworking to boost dimensional stability and mechanical robustness, particularly beneficial for aluminum that has undergone casting, forging, or welding processes. Vibratory stress relief specifically targets residual stress that persists even after the initial stress-inducing actions have concluded. Residual stress typically arises from inelastic deformations, temperature differentials, and structural transformations. For instance, in welding, localized heating causes expansion, followed by varying rates of contraction during cooling, leading to residual stress formation.
Vibratory stress relief finds significant application in intricate components with stringent dimensional or geometric tolerances and in heavily loaded workpieces like lifting yokes, crane bases, and rolling mills. By honing in on the metal’s resonant frequency, VSR optimizes stress relief by harmonizing induced stresses with existing residual stresses. This harmonic action induces plastic deformation, ultimately aiding in stress alleviation within the aluminum material.