Aluminum, a versatile and widely used metal in various industries, requires rigorous testing to ensure its quality and integrity. One such method is Ultrasonic Testing (UT), a non-destructive testing technique that is commonly employed to assess the properties of aluminum plates.
What Is Aluminum Ultrasonic Testing?
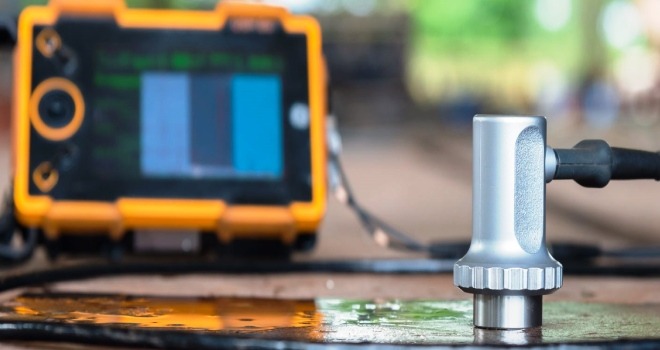
Aluminum Ultrasonic Testing is a method that involves introducing high-frequency sound waves into materials for non-destructive inspection. The sound waves typically range between 0.1 MHz and 50 MHz. In industrial applications, this technology is utilized to determine the dimensions of the material being tested, which is crucial for tasks such as monitoring pipework corrosion.
UT testing is commonly employed in industries working with stainless steel, aluminum, and various other metals. It can be used to assess a range of materials including forgings, castings, wrought and cast plate, extrusions, and bar stock.
A typical Ultrasonic Testing inspection system consists of essential components such as a pulser/receiver, transducer, and display devices. The transducer directly contacts the material under test, often requiring a couplant or water immersion for effective connection. The pulser generates high-voltage electrical energy, which the transducer converts into high-frequency ultrasonic energy that is transmitted into the material being tested.
Aluminum UT Inspection Methods
Aluminum UT inspection employs two key methods for receiving ultrasound waveforms: reflection and attenuation.
In the reflection method of Aluminum UT inspection, the transducer functions by both sending and receiving pulsed waves. Any imperfections within the material reflect these waves back to the transducer, allowing for the detection of flaws such as cracks or voids based on the reflected signals.
In attenuation ultrasound, a transmitter directs ultrasound waves through one side of the material to a receiver placed on the opposite side. Imperfections in the material, such as voids or inclusions, absorb or scatter the sound waves, resulting in a decrease in the amount of transmitted sound. By analyzing the attenuation of the ultrasound waves, inspectors can identify and characterize defects within the material being tested.
How To Test For Aluminum?
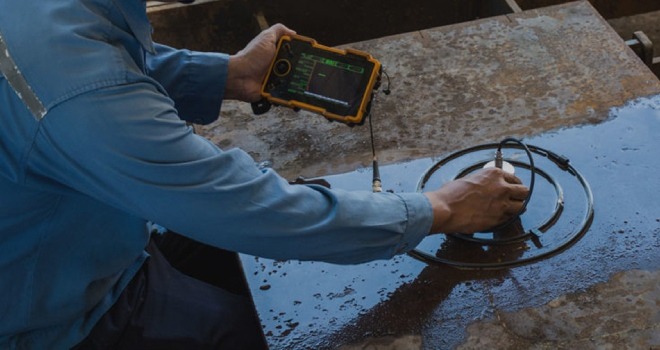
To test aluminum plates using ultrasonic methods, traditionally, two primary approaches have been employed. The first method, known as contact ultrasound, utilizes a couplant to enhance the effectiveness of the testing signal.
Contact ultrasound operates based on the concept that sound waves travel directionally through a material. Upon encountering a crack, void, or inclusion within the aluminum plate, the sound wave undergoes alteration, resulting in a change in the amplitude detected by the testing machine. The time taken for the ultrasonic signal to travel directly correlates to the distance covered within the material, allowing for the identification of imperfections in terms of their location, size, and orientation.
Contact ultrasonic testing relies on the couplant to ensure optimal contact between the signal transmitter and the test material, thereby improving efficiency. Typically, the couplant used is an oil or gel that acts as a seal between the two components.
In contrast, immersion ultrasound systems are sophisticated devices that come equipped with various automated features to enhance precision. These systems incorporate large tanks in which the aluminum plate being tested is immersed. The liquid environment in immersion testing serves a similar function to the couplant in contact UT testing, facilitating accurate and thorough inspection of the aluminum plates.
Benefits Of Ultrasonic Testing For Aluminum Plates
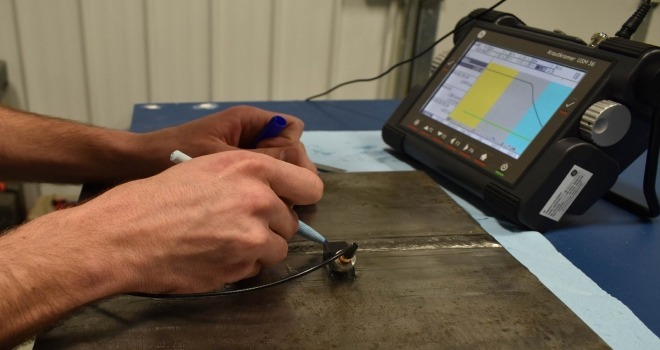
Non-Destructive Testing: Ultrasonic testing for aluminum plates is non-destructive, preserving the integrity of the material while providing insights into internal structures and potential defects without altering or compromising the plates’ usability.
High Sensitivity to Defects: The method’s high sensitivity enables the detection of minuscule flaws such as micro-cracks, voids, and inclusions that may not be visible to the naked eye, ensuring a comprehensive examination of the aluminum plates for even the smallest imperfections.
Precise Thickness Measurements: UT testing offers precise measurements of the thickness of aluminum plates, allowing for accurate assessment of material integrity and identifying any variations that might impact performance or structural stability.
Versatility Across Plate Variations: Whether dealing with different sizes, shapes, or thicknesses of aluminum plates, ultrasonic testing remains adaptable and effective, making it a versatile solution for a variety of plate configurations.
Efficient Inspection Process: The relatively quick nature of ultrasonic testing enables efficient inspection of aluminum plates, facilitating rapid evaluation of large quantities of material without compromising the thoroughness of the assessment.
Cost-Effectiveness through Early Detection: By detecting defects early in the inspection process, ultrasonic testing helps prevent potential failures or accidents that could result in costly repairs, replacements, or production delays, ultimately saving on maintenance expenses.
Buy Quality Aluminum Plates From Us
Being a foremost producer of top-tier aluminum plates, we go the extra mile by implementing state-of-the-art testing methodologies, notably ultrasonic testing, to uphold unparalleled quality benchmarks. Rely on us for aluminum plates that not only meet but surpass the exacting demands of your projects, boasting flawless integrity and performance. Elevate your standards and entrust us as your go-to supplier for premium aluminum plates that embody precision, durability, and reliability, setting the foundation for the success of your ventures.