Aluminum forging, a vital process in manufacturing, renowned for versatility, strength, and lightweight properties. This guide delves into aluminum forging, covering applications, benefits, and considerations, leveraging the expertise of an experienced aluminum fabricator.
What Is Aluminum Forging?
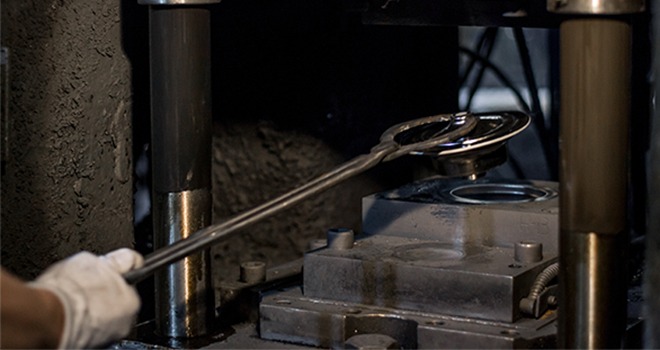
Aluminum forging is a fundamental process in manufacturing, essential for shaping aluminum alloys using pressure and heat to create durable products. By compressing aluminum billets under high pressure, this method enhances component strength. Temperature control is crucial, varying from below the recrystallization point to slightly above it.
Various forging techniques, such as open and closed die forging, cater to different products and applications. Aluminum’s lightweight nature, strength, corrosion resistance, and forgeability make it versatile. Compared to carbon steel, aluminum alloys have lower deformation resistance at room temperature and are sensitive to temperature variations.
While casting is common for shaping aluminum, forging is preferred for refining metallurgy through deformation energy. This process eliminates imperfections, enhances internal structures, and improves product durability and toughness. Aluminum forging’s impact lies in its ability to transform aluminum alloys into high-performance components, addressing diverse industrial needs with strength and precision.
At What Temperature Is Aluminum Forged?
Aluminum forging is commonly carried out at controlled die temperatures ranging from 650 to 800°F (343.3 to 426.7°C) for near-net forging applications. In conventional forging processes, a wider temperature range is acceptable to meet different specifications and production needs.
Aluminum Forging Types
Aluminum forging methods cover cold forging, hot forging, drop forging, rolled ring forging, open die forging, and closed die forging. These techniques are tailored to specific applications and material properties: cold forging offers precise control at or near room temperature, while hot forging enhances ductility at elevated temperatures. Drop forging, rolled ring forging, open die forging, and closed die forging each bring unique strengths to the aluminum forging process.
Cold Forging Aluminum
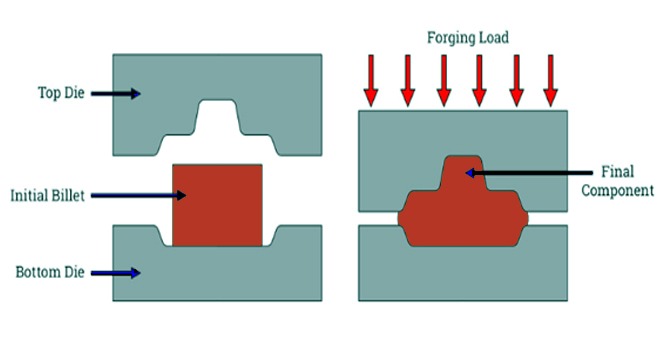
In the realm of metalworking, cold forging aluminum emerges as a pivotal technique for shaping the metal into intricate and multifaceted forms. This process capitalizes on aluminum’s inherent plasticity, enabling permanent deformation at room temperature. Unlike traditional cutting methods, cold forging aluminum expedites production, eliminating wasteful shavings while effortlessly crafting complex designs in two dimensions. By deforming aluminum below its recrystallization threshold, cold forging aluminum efficiently yields finished components with minimal need for additional finishing. Through the application of vertical presses, this cost-effective method ensures meticulous dimensional control and a flawless surface finish, making it indispensable in the fabrication of a diverse range of aluminum parts such as alternators, gears, and valves, underscoring its adaptability and economic advantages.
Hot Forging Aluminum
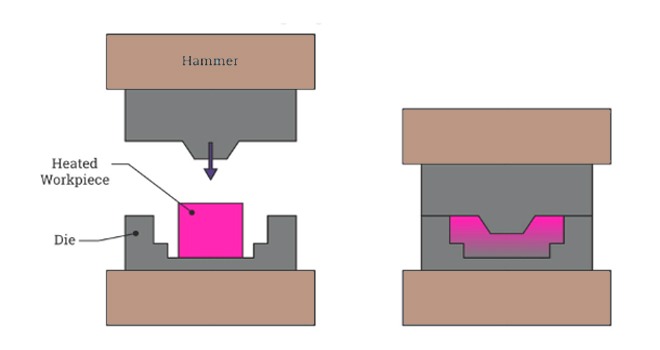
In the process of hot forging aluminum, the metal is heated to temperatures between 350°C and 500°C (662°F and 932°F), reaching its critical recrystallization point. Subsequently, under pressure from forging equipment, the heated aluminum workpiece is shaped and molded into a die. This technique results in a final product featuring enhanced strength, durability, and a finer grain size. The lightweight quality, impressive strength-to-weight ratio, and exceptional thermal and electrical conductivity of hot forged aluminum contribute significantly to its widespread acceptance.
Critical to the process of hot forging aluminum are heat and pressure. Maintaining elevated temperatures is crucial to prevent strain hardening during deformation. Forging dies are heated to match the workpiece’s temperature or slightly below it to ensure consistent high temperatures. Through successive hammering and stamping, the aluminum workpiece is meticulously shaped until it achieves the desired form, aided by the heated dies to facilitate material flow.
Drop Forging Aluminum
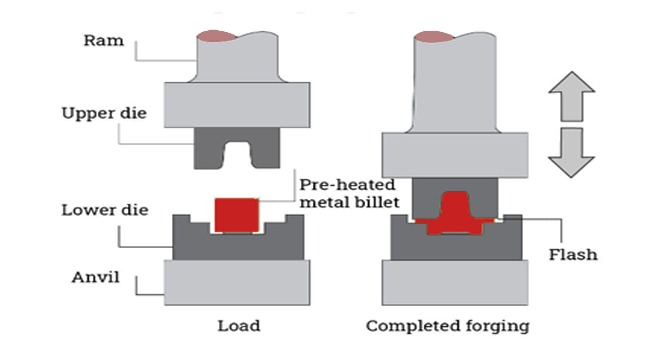
Drop forging aluminum is a method that involves shaping an aluminum workpiece by hammering it between two halves of a die, making it an ideal choice for the mass production of aluminum components. In this process, the upper die half, attached to a hammer, interacts with the lower die half positioned on an anvil. The heated aluminum workpiece is positioned in the lower die half on the anvil, and continuous pressure is applied to compress the workpiece until it completely fills the die cavity. Any excess aluminum, referred to as flash, is extruded through the openings between the die halves and can be collected for reuse.
Given its lightweight nature, aluminum is particularly well-suited for drop forging, with a focus on alloys from the 6000 and 7000 series. Following the drop forging process, the flash is removed from the workpiece, which may then undergo further treatments.
Drop forging enhances the strength, toughness, and fatigue resistance of aluminum, ensuring precise dimensional accuracy and uniformity in the final product. This cost-effective method minimizes waste and is proficient in producing intricate and detailed shapes efficiently.
Rolled Ring Forging Aluminum
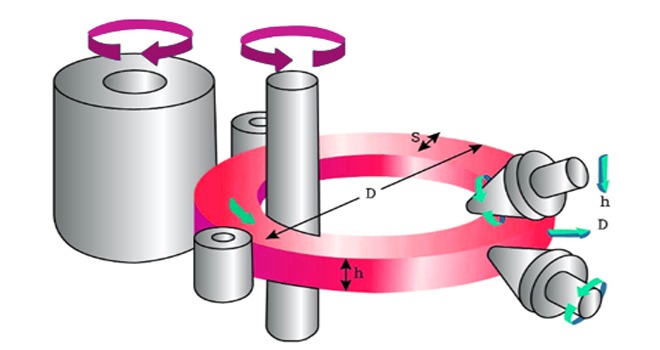
Rolled ring forging with aluminum is a specialized process that involves creating seamless rings from billets or cylinders. This method commences with upsetting the billet, which involves decreasing its height while expanding its diameter to achieve the final dimensions needed for the ring. Rolled ring forging utilizes an open die technique, where the billet is heated above its recrystallization temperature. The upsetting phase readies the billet by applying horizontal pressure along its length, causing it to expand beyond the press area. Heat is applied to the billet to soften it and increase its ductility, thereby modifying the metal’s grain structure. In order to form the ring, the workpiece must be pierced to create a central hole, typically achieved through punching or shearing. This process results in a donut-shaped piece that can be placed over a mandrel and shaped by rollers into the final ring.
The workpiece is gradually rotated and pressed against the drive roller, adjusting the inner and outer diameters (ID and OD) to match the final specifications. As the workpiece revolves, the mandrel presses against the donut’s interior, compressing the ring walls to reduce their thickness. The exceptional toughness, tensile strength, and fatigue resistance of aluminum make it a prime candidate for rolled ring forging. Unlike many other metals, forged aluminum yields a superior surface finish that is both smooth and visually appealing.
Open Die Forging Aluminum
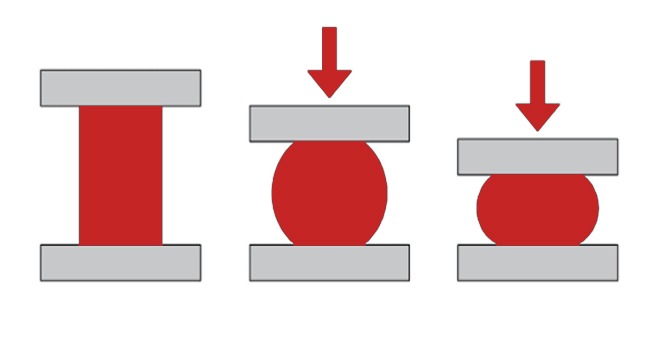
Open Die Forging with Aluminum is a technique where dies that do not enclose the material fully are used to shape aluminum. The process involves stamping, hammering, and shaping an aluminum billet until it matches the die’s form. As the material isn’t entirely enclosed, additional processing is often required to achieve the final shape. This method is typically employed for creating simple components like discs, sleeves, cylinders, and shafts.
Through repeated impacts on the aluminum billet, open die forging refines the grain structure of aluminum parts, enhancing their fatigue resistance and strength. By eliminating voids that could weaken a part, this technique ensures product effectiveness.
Closed Die Forging Aluminum
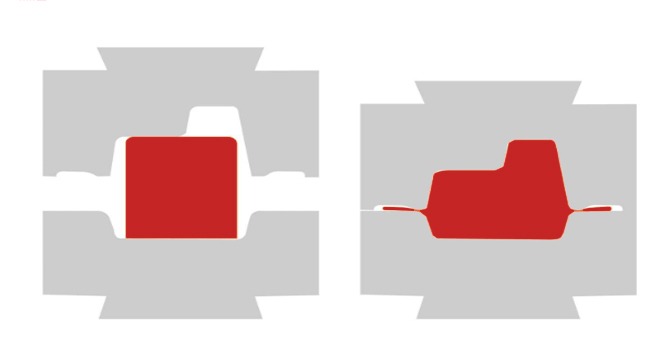
Closed die forging of aluminum involves enclosing the blank or billet within dies to shape the final product, contrasting with open die forging. This process can be single or multi-staged based on complexity. Alloys for this forging are heat-treated at various temperatures as per their composition.
The method includes shaping the billet between upper and lower die halves, with the lower half on an anvil and the upper half on a hammer. Precise deformation aligns grain flow with stress direction, refining the billet’s microstructure.
Primarily used for high-volume production due to die costs, closed die forging ensures precise dimensions and allows for secondary machining to achieve tight tolerances. Products exhibit consistent accuracy, reducing the need for additional finishing. The process yields aluminum forgings with superior mechanical properties and structural integrity, ideal for large-scale production runs with enhanced cost efficiency and improved production rates.
What Is The Best Aluminum For Forging?
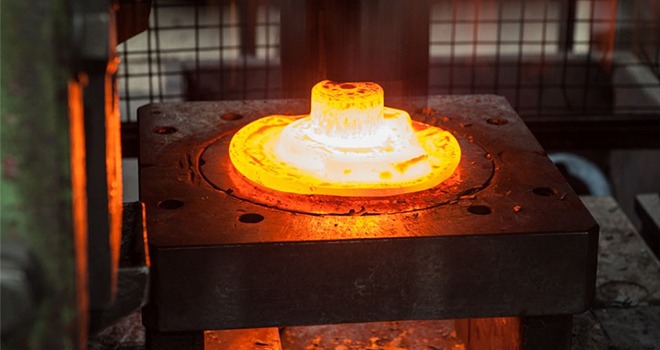
Aluminum alloys play a crucial role in forging applications, each offering distinct advantages based on specific requirements. Among them, forged aluminum 7075 stands out for its exceptional strength, with zinc, copper, and magnesium as primary elements. This alloy, known for its high tensile strength of 83,000 psi and resistance to stress corrosion cracking, is favored in high-stress structural components.
Forged aluminum 7075 is extensively used in airframe construction, aerospace, and industries demanding robust components. Its forging properties enable the creation of parts with superior strength and durability, making it a preferred choice for applications where reliability under intense conditions is essential. The alloy’s remarkable strength, forgeability, and resistance to stress corrosion cracking make it a top candidate for critical forging applications requiring unmatched strength and performance.