Aluminum is a versatile and widely used material known for its lightweight properties and durability. However, to truly maximize the potential of aluminum in various applications, the importance of aluminum finishes cannot be overlooked. These finishes not only protect but also enhance the performance of aluminum products in numerous ways.
What Is Aluminum Finishes?
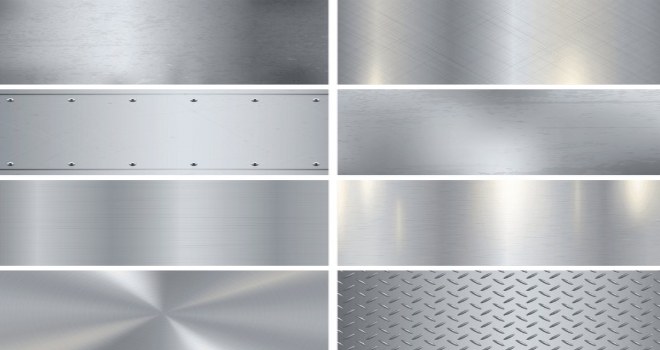
Aluminum finishes refer to the surface treatments applied to aluminum to improve its appearance, durability, and performance. These aluminum surface finishes can include processes like anodizing, powder coating, painting, polishing, and other surface treatments that are designed to protect the aluminum from corrosion, enhance its aesthetics, provide color options, improve durability, and even optimize functional properties like conductivity or heat dissipation. The choice of finish can depend on the specific requirements of the application, such as the desired appearance, environmental conditions, and performance expectations.
Why Aluminum Need Surface Treatment?
Aluminum necessitates surface treatments for several reasons. Firstly, these treatments enhance corrosion resistance, crucial for aluminum’s longevity when exposed to moisture and harsh environments. Additionally, aluminum surface finishes like anodizing improve durability by creating a protective layer that increases wear resistance. Aesthetically, treatments such as painting or powder coating enhance the visual appeal, allowing for customization and versatility. Functionally, certain treatments can enhance properties like conductivity or thermal performance, expanding the material’s potential applications. Moreover, aluminum surface treatments can facilitate easier cleaning, essential in hygiene-sensitive industries. Lastly, treatments aid in improving adhesion, ensuring better bonding in composite structures or assemblies.
Types Of Aluminum Finishes
Aluminum can be finished in various ways, including Mill Finish, Anodizing, Powder Coating, PVDF Coating, Liquid Paints, Mechanical Finishing, Wood Grain Aluminum, Alodining, and Bright Dipping. These methods offer a range of options to enhance the appearance and performance of aluminum surfaces in diverse applications.
Aluminum Mill Finish
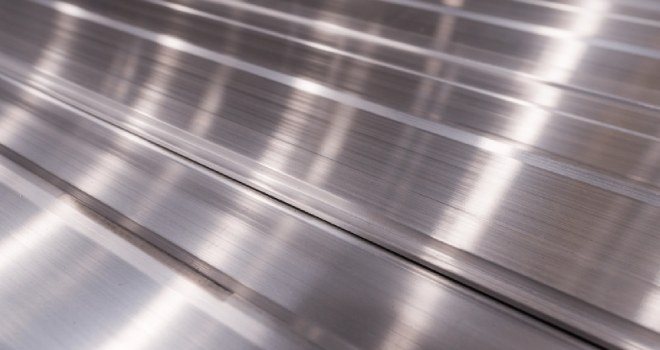
Aluminum extrusions initially bear a Mill Finish, showcasing their state post-extrusion. This finish reveals die and tooling marks, a lackluster appearance, oxidation, and faint white “rust”. Primarily suited for cost-driven projects with short lifespans, a Mill Finish is chosen when aesthetics are inconsequential. Alternatively, exploring different aluminum finishing options is recommended for long-lasting and visually appealing results. Essentially, Mill Finish aluminum denotes the untreated, unpolished state of the metal, maintaining a raw and somewhat lackluster surface. Retaining properties akin to cast aluminum, this untouched form often exhibits soft spots and varied appearances based on the alloy and intended application.
Aluminum Anodizing Finish
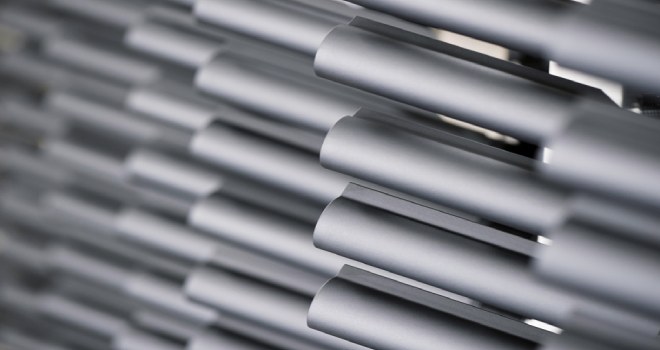
Aluminum Anodizing Finish is a widely utilized method to enhance aluminum parts’ corrosion and wear resistance while offering additional benefits like improved heat dissipation and dye acceptance. Unlike traditional coatings, anodizing triggers a natural growth of the aluminum oxide layer through an electrochemical process, fortifying the material against environmental factors and enabling dye absorption. Although color choices are more limited compared to powder coating, anodizing remains a preferred aluminum surface finsh for profiles, creating durable, visually pleasing, and corrosion-resistant oxide layers of varying thicknesses. This integrated oxide coating ensures longevity and superior performance, showcasing vibrant colors and prolonged appearance retention for anodized aluminum components.
Aluminum Powder Coating
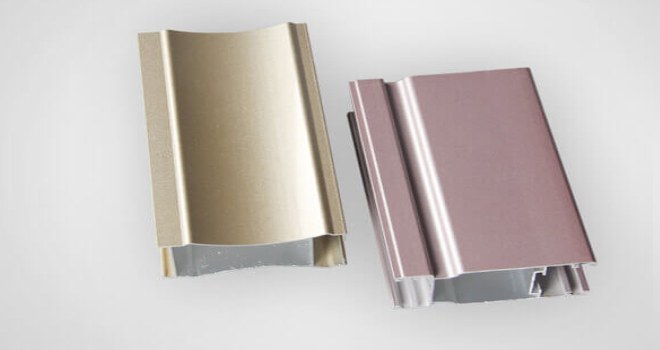
Aluminum Powder Coating offers vibrant, long-lasting colors with high UV resistance, making it a preferred choice for many product designers. In this process, aluminum parts undergo cleaning and preparation before a dry paint powder is applied using an electrostatic gun, ensuring an even finish after baking to melt and cure the coating.
While not as durable as anodized aluminum, powder coatings boast exceptional appearance and corrosion resistance when the coating remains intact. Compared to liquid painting, powder coating is environmentally friendly, devoid of solvents containing volatile organic compounds (VOCs). Ideal for products needing both decorative and protective finishes, powder coating involves applying a protective layer through an electrostatic process.
By using a specialized spraying gun to negatively charge powder particles and applying them to an earthed surface, a solid connection forms between the aluminum and the coating upon curing. Despite its environmental benefits, powder coating may result in a slightly textured finish due to the granules used in the process.
Aluminum Liquid Paint
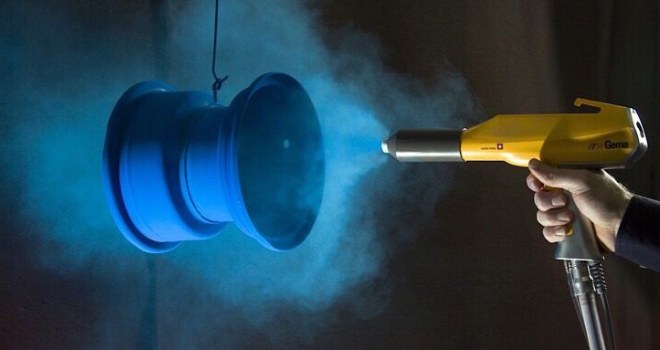
Liquid paints, unlike PVDF, provide a flexible solution for obtaining exact colors, especially beneficial for smaller production runs. They offer a diverse range of color options and can be custom mixed in quantities tailored to specific product requirements.
Nevertheless, the inclusion of solvents containing volatile organic compounds (VOCs) in these paint types poses risks to both health and the environment. To mitigate these dangers associated with such aluminum surface finishes, painters must implement VOC abatement systems.
Aluminum PVDF Coating
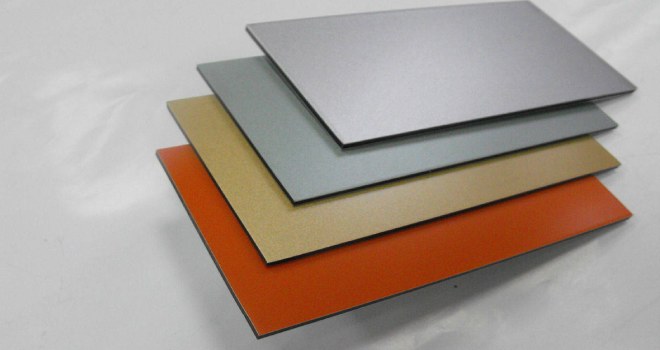
The application of Aluminum PVDF Coating involves using resin-based coatings with color pigment particles embedded, typically done in factory settings to achieve a range of matte colors on aluminum surfaces.
Known for their outstanding resistance to corrosion, fading, and chemicals, PVDF coatings are particularly well-suited for outdoor applications such as aluminum wall cladding. Unlike powder coatings, they do not require baking for curing and can be applied in thinner layers.
While PVDF coating may generate more waste compared to powder coating, it is recognized for its eco-friendliness due to the absence of harmful volatile organic compounds (VOCs).
Aluminum Mechanical Finishing
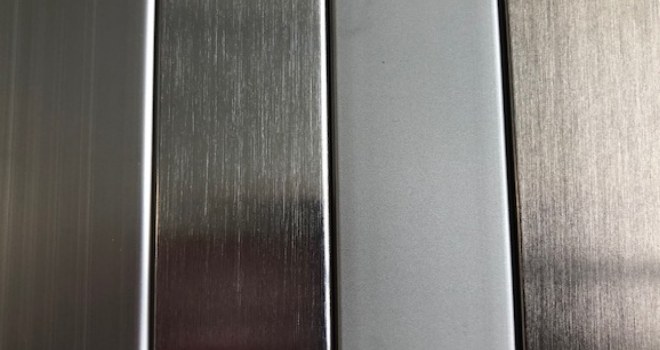
Aluminum Mechanical Finishing involves a range of methods used to modify the surface of aluminum components. Techniques such as abrasive blasting, grinding, and polishing are commonly employed in this process.
Instead of utilizing chemicals, mechanical force is applied through abrasive media to refine the surface of the aluminum. This approach can enhance the appearance of the material or prepare it for further finishing treatments.
Aluminum Alodining
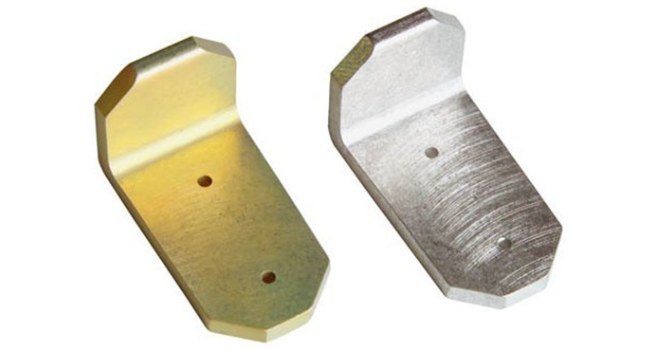
Aluminum Alodining is a cost-effective option compared to anodizing, enhancing the protective oxide layer on aluminum surfaces to boost corrosion resistance. While Alodine chem film may not match the durability of anodized aluminum, its notable electrical conductivity is advantageous for specific applications.
It is essential to consider that the Alodine solution is less environmentally sustainable than other available options. Alodine finish, or chem film, is a suitable treatment for reinforcing the oxide film on aluminum surfaces. This process involves immersing the aluminum part in a controlled chemical bath for a specified duration to develop the Alodine film on its surface.
This method provides enhanced corrosion resistance for machined aluminum parts and serves as a more economical alternative to anodizing. Although it may not offer the same level of durability as anodized coatings, the chem film is particularly beneficial for applications requiring increased electrical conductivity.
Aluminum Bright Dipping
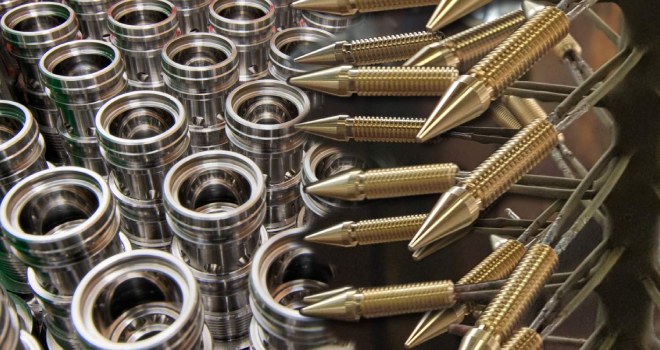
Aluminum Bright Dipping is a technique used to achieve a highly polished surface on aluminum parts. This process involves immersing the parts in acid to smooth out surface imperfections, resulting in a mirror-like finish.
While bright dipping can be necessary for certain products that require a flawless appearance, it is important to note that this process can be hazardous and environmentally harmful. Additionally, it is most effective with specific aluminum grades, such as the 6463 alloy.
This aluminum finishing method is popular for creating shiny finishes on items like food and beverage containers. However, the chemicals used in bright dipping come with risks and are not suitable for all aluminum alloys.
How Do Aluminum Finishes Enhance Aluminum Performance?
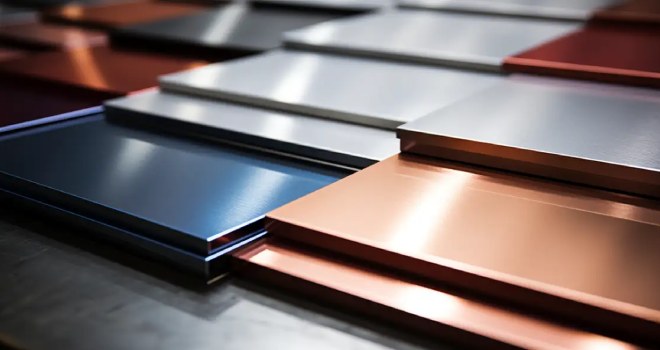
Each specific aluminum finish excels in enhancing distinct aspects of aluminum performance, catering to particular needs such as corrosion resistance, durability, aesthetics, chemical resistance, cost considerations, and unique design requirements.
Corrosion Resistance
In enhancing corrosion resistance, anodizing establishes a protective oxide layer that significantly boosts the aluminum’s ability to fend off corrosion. On the other hand, PVDF coating not only amplifies corrosion resistance but also furnishes enduring protection against environmental elements.
Durability and Scratch Resistance
In terms of durability and resistance to scratches, powder coating stands out with remarkable toughness and scratch resistance, safeguarding aluminum products, especially those enduring high-traffic environments. Conversely, anodizing boosts scratch resistance and overall durability by enhancing surface hardness, making it a top choice for products susceptible to abrasion.
Aesthetic Appeal
When it comes to aesthetic appeal, liquid paint presents a wide spectrum of colors and finishes, elevating the visual allure of aluminum products and enabling tailored designs to meet specific aesthetic demands. And anodizing diversifies the color palette and finish options, enriching the aesthetic flexibility of aluminum surfaces, particularly favored in architectural applications that seek distinctive appearances.
Chemical Resistance and Longevity
Regarding chemical resistance and longevity, PVDF coatings fortify aluminum surfaces against harsh environments, enhancing resistance to chemicals and preserving colors, thereby prolonging the lifespan of the material. In comparison, Alodining enhances resistance to corrosion and chemicals, effectively extending the durability of aluminum components in demanding conditions, establishing it as a dependable option for applications necessitating robust protection.