When deciding between Aluminum 6061 T6 and 6061 T651 for your project, understanding the differences is crucial. Aluminum 6061 is a versatile material known for its strength and corrosion resistance, making it a popular choice in various industries. The T6 and T651 designations refer to specific tempering processes that affect the material’s properties.
What Is 6061 T6 Aluminum?
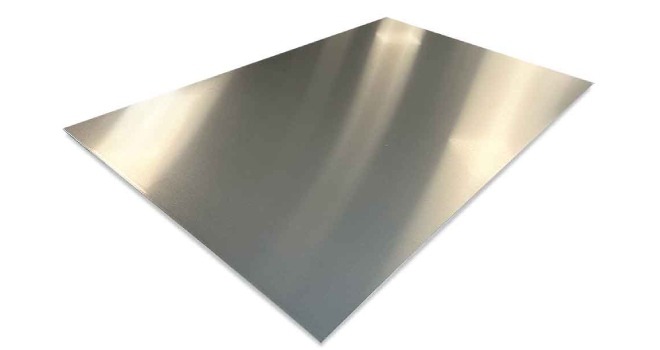
6061 T6 aluminum is a high-strength alloy renowned for its exceptional mechanical properties, widely applied across diverse industrial sectors. Through tempering processes, like T6, its qualities can be further enhanced, boasting excellent corrosion resistance and weldability.
Mechanical Properties Of 6061-T6 Aluminum
Upon the application of the T6 temper to aluminum, such as in the case of 6061-T6 aluminum, the material’s mechanical properties experience a notable improvement. In comparison to 0-tempered aluminum, the yield strength of 6061-T6 aluminum increases significantly, nearly quadrupling. For example, while 6061 0-temper demonstrates a yield strength of 55 MPa and a tensile strength of 125 MPa, the T6 temper boosts these values considerably. Specifically, 6061-T6 aluminum exhibits a minimum yield strength of 240 MPa and a minimum tensile strength of 290 MPa, showcasing its superior mechanical characteristics and suitability for applications requiring enhanced strength and resilience.
6061-T6 Aluminum: Advantages and Disadvantages
When considering 6061-T6 aluminum, it is important to weigh its advantages and disadvantages.
Advantages of 6061-T6 Aluminum
High Strength and Lightweight: The T6 temper endows 6061-T6 with exceptional strength while maintaining its lightweight nature, ideal for applications demanding robustness without adding excess weight.
Excellent Corrosion Resistance and Weldability: T6 tempering enhances corrosion resistance, crucial for longevity in various environments, and facilitates easy welding processes, ensuring efficient fabrication.
Improved Formability and Machinability: Compared to other high-strength aluminum alloys, 6061-T6 offers superior formability and machinability, simplifying shaping and processing tasks in manufacturing.
Disadvantages of 6061-T6 Aluminum
Complex Heat Treatment Process: Achieving the desired properties in 6061-T6 requires a meticulous heat treatment process, necessitating precise control over parameters like heating rate, time, and temperature, adding complexity to the manufacturing process.
Increased Cost: The specialized heat treatment involved in T6 tempering makes 6061-T6 more expensive compared to alternatives like T5, impacting overall project costs.
Reduced Ductility: While T6 temper enhances strength, it can lead to reduced ductility in the material, potentially affecting its ability to deform without breaking under stress.
What Is Aluminum Alloy-T651?
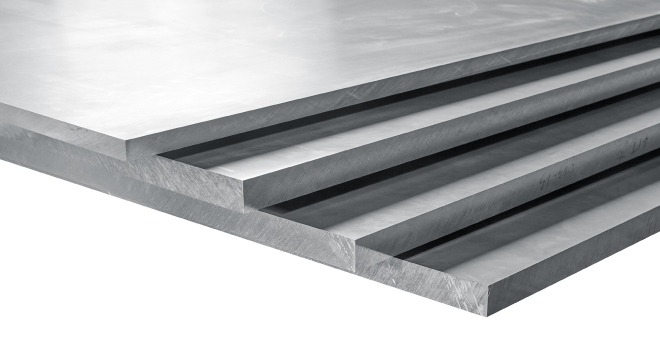
6061-T651 aluminum represents an advancement of the T6 temper found in aluminum alloys, providing superior processability compared to conventional T6 tempered alloys. Specifically advantageous for machining tasks such as grinding, polishing, and cutting, the T651 temper stands out as a valuable option. The process of attaining the T651 temper generally entails the formation of a solid solution, subsequent stress relief through material stretching, and culminates in artificial aging to achieve this precise temper.
6061 T651 Mechanical Properties
In the domain of materials engineering, 6061 T651 aluminum emerges as a stalwart with its impressive mechanical characteristics. Boasting an Ultimate Tensile Strength of 310 MPa and a Yield Tensile Strength of 276 MPa, this alloy epitomizes resilience. Complemented by a Fatigue Strength of 96.5 MPa and a Shear Strength of 207 MPa, 6061 T651 embodies strength and durability.
One of the defining attributes of 6061 T651 aluminum is its capacity to uphold a high strength-to-weight ratio and hardness post-tempering, rendering it exceedingly suitable for a spectrum of processing applications. However, as external forces dissipate during fabrication, internal stresses persist. These residual stresses trigger a recovery effect, leading to observable alterations in the material’s dimensions—a dynamic interplay between external manipulation and internal responses in the intricate world of material science.
Difference Between 6061 T6 And T651
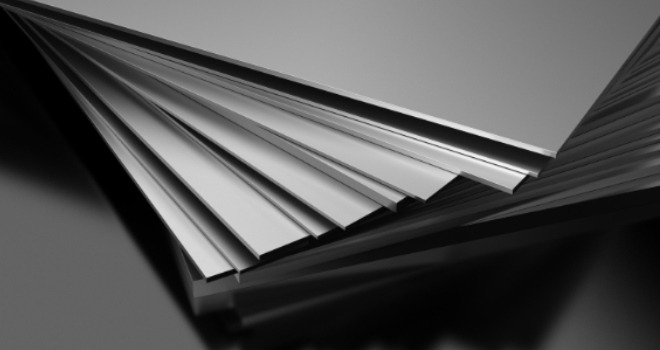
When we look at 6061 T6 and 6061-T651 aluminum alloys, we notice several differences that stem from the refining of the tempering process in the latter:
6061 T6 vs 6061 T651 - Strength Analysis
In the realm of tensile strength, 6061 T651 often edges out 6061 T6, thanks to its advanced tempering techniques.
Deformation Resistance
Notably, the yield strength of 6061-T651 typically surpasses that of 6061 T6, rendering it more resilient against deformation during machining operations.
Machinability Focus
When it comes to machinability, 6061 T651 shines, offering a superior option for shaping tasks that demand precision compared to 6061 T6.
6061 T6 vs 6061 T651 - Distortion and Stability
Post-processing, 6061-T651 exhibits remarkable stability with reduced distortion tendencies, making it an ideal candidate for applications requiring complex shapes and meticulous dimensional accuracy. In contrast, 6061 T6, while offering commendable strength, may experience noticeable distortions during machining processes due to internal stresses.
Cost Considerations
An essential factor to weigh is the cost implications. 6061 T651, with its additional stress-relieving processes, often comes at a higher price point compared to 6061 T6. This cost disparity reflects the enhanced properties and machining advantages offered by the T651 temper.
6061 T6 vs 6061 T651 - Manufacturing Techniques
The manufacturing methods for these alloys diverge significantly. 6061 T6 involves a heat treatment process that includes heating up to 980°F, quenching in water, and subsequent artificial aging. On the other hand, 6061 T651 aluminum undergoes additional stretching post-quenching to eliminate residual stresses, enhancing its dimensional stability and machinability.
Aluminum 6061 T6 vs T651: Which Is Better?
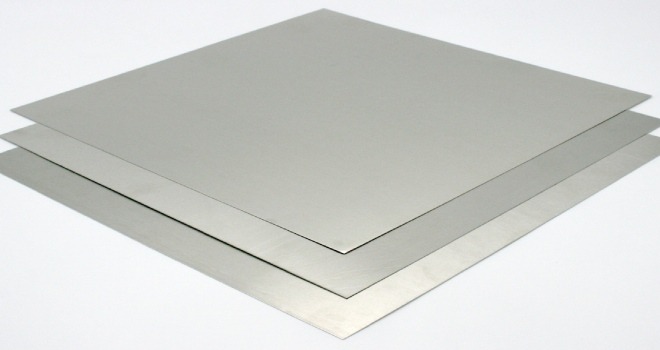
In the realm of aluminum alloy selection, the choice between 6061 T6 and 6061 T651 often serves as a critical decision point for engineers and manufacturers alike. Each variant offers distinct advantages tailored to specific application requirements, showcasing nuanced differences in properties and performance characteristics.
6061 T6 Applications
- Strength-Centric Needs: Aluminum 6061 T6 is a reliable choice for applications prioritizing high strength and commendable corrosion resistance, particularly when intricate machining isn’t a primary requirement. Its robust nature makes it ideal for projects where durability and resistance to external elements are essential.
- Structural Components: Widely utilized in structural applications, 6061 T6 is favored for its exceptional strength-to-weight ratio, making it a go-to option for constructing frameworks, load-bearing elements, and components that demand resilience and structural integrity.
- Automotive and Aerospace: In the automotive and aerospace industries, where components are subjected to rigorous conditions and must withstand high stresses, 6061 T6 shines. Its properties make it suitable for aircraft fittings, marine hardware, automotive parts, and other critical applications where strength plays a pivotal role.
6061 T651 Applications
- Precision Machining: 6061 T651 aluminum stands out in projects that necessitate precision machining, intricate shapes, and stringent accuracy requirements. The enhanced machinability of T651 makes it a preferred choice for tasks demanding fine detailing and complex geometries.
- Dimensional Stability: For applications where maintaining dimensional stability and minimizing post-processing distortions are paramount, 6061-T651 excels. Its stress-relieving stretching process after heat treatment ensures improved dimensional accuracy, making it ideal for components where precision is non-negotiable.
- Cost Considerations: While slightly pricier than 6061 T6, the cost differential is often justified by the efficiency gained in machining processes. The improved machinability and dimensional stability of 6061 T651 can lead to long-term cost savings by reducing machining times and waste, particularly in projects where precision and minimal distortion are critical factors in component production.