Aluminum extrusion stands as a pivotal manufacturing process that enables the creation of a vast array of products across industries. From intricate profiles to specialized shapes, the versatility of aluminum extrusion types plays a key role in modern manufacturing and design.
Understanding Aluminum Extrusion
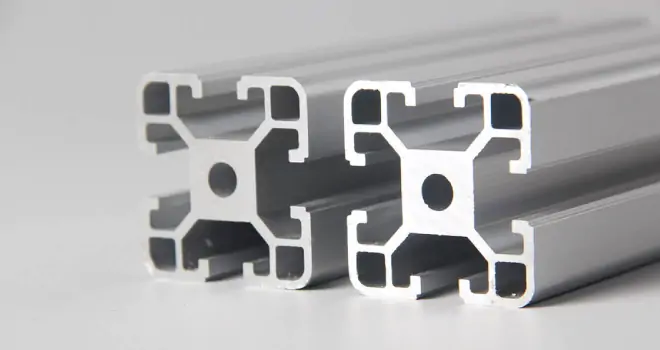
At its core, aluminum extrusion involves shaping aluminum alloys into profiles by forcing the material through a die. This process allows for the creation of complex shapes with precision and consistency, making it a preferred choice for a wide range of applications.
Different Types of Aluminum Extrusion Manufacturing Processes
Aluminum extrusion offers a diverse array of techniques, each tailored to specific needs and applications. Understanding the nuances of various extrusion methods is essential for optimizing the manufacturing process and achieving desired outcomes.
Direct Extrusion
Direct extrusion is a fundamental method in aluminum extrusion, characterized by the straightforward process of pushing a billet through a die to produce a profile. This technique is highly cost-effective and efficient, making it ideal for creating profiles with simple shapes. Direct extrusion is widely used in industries where streamlined production processes are paramount, offering a reliable and economical solution for manufacturing a variety of aluminum profiles.
Indirect Extrusion
In indirect extrusion, a more intricate approach is taken where the die moves while the billet remains stationary. This method allows for the creation of highly detailed and complex profiles with a level of precision that surpasses that of direct extrusion. By keeping the billet stationary, indirect extrusion offers better control over the extrusion process, resulting in profiles that exhibit superior surface finish and dimensional accuracy. Industries that require intricate profiles with specific design requirements often opt for indirect extrusion to achieve the desired results.
Impact Extrusion
Impact extrusion involves striking a billet with a punch to force the metal to flow around it and form the desired shape. This method is commonly employed in the production of parts such as cans and containers, where intricate shaping and precise detailing are essential. Impact extrusion is favored for its ability to create profiles with varying wall thickness and intricate designs, making it a versatile choice for applications that demand high precision and complex geometries.
Hydrostatic Extrusion
Hydrostatic extrusion utilizes pressurized fluid, typically hydraulic oil or water, to push the billet through the die. This method is particularly suited for materials that are challenging to extrude using traditional techniques due to their high strength or unique properties. By applying uniform pressure to the billet, hydrostatic extrusion ensures consistent material flow and facilitates the production of profiles with enhanced mechanical properties and structural integrity. Industries requiring profiles with superior strength and dimensional accuracy often rely on hydrostatic extrusion to meet their specific requirements effectively.
What's The Difference Between Extrusion Profile And Common Profile?
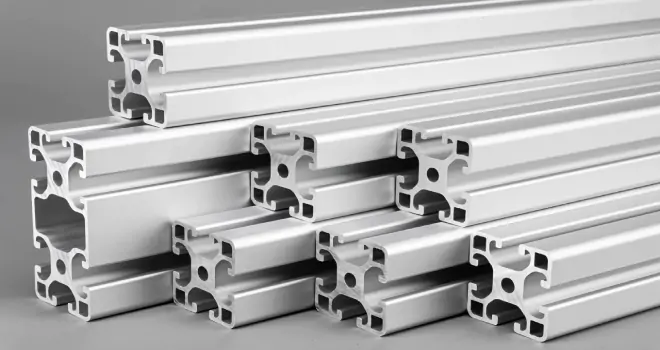
In the realm of metal shaping, extrusion profiles and common profiles stand out as distinct methods with unique characteristics.
Manufacturing Process
Extrusion profiles are carefully crafted through a sophisticated process involving the extrusion of metal material at high temperatures through one or more porous dies. Common profiles are shaped using methods like cold bending or cold rolling, skipping the need for heat treatment during production, thus simplifying the manufacturing process.
Precision in Dimensional Control
The precision in dimensional control sets these profiles apart. Extrusion profiles, thanks to hot extrusion technology, achieve exceptional dimensional accuracy, intricate shapes, and smooth surface finishes efficiently. In contrast, common profiles, due to their simpler manufacturing process, exhibit lower dimensional precision compared to their extruded counterparts.
Applications
Extrusion profiles find their niche in applications that demand precision and complexity. They are commonly used in crafting small components, connectors, linear guides, and braking systems across various industries such as construction (door and window frames, home decor, and aluminum alloy curtain walls), transportation (ship structures, vehicle bodies, and carriages), and mechanical fields (factory automation, gearboxes, and hydraulic cylinders).
Common profiles, on the other hand, are versatile in applications such as home furnishings, appliances, doors, and windows, where the intricate shapes and high precision of extrusion profiles are not necessary. Their simplicity in production makes them well-suited for a range of everyday uses that do not require the complexity of extrusion techniques.
Aluminum Extrusion Types
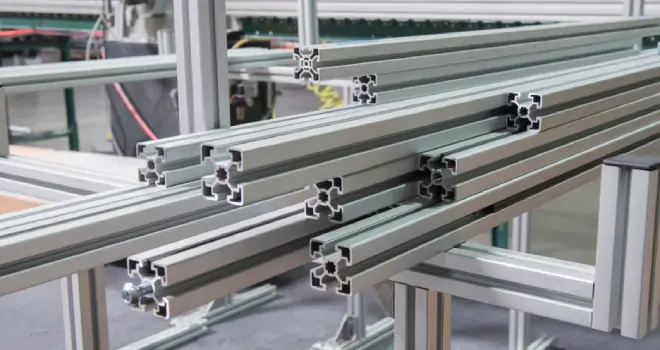
Aluminum extrusion types encompass a diverse array of profiles tailored to different industrial and commercial requirements.
Aluminum Channel
Aluminum channels are U-shaped extrusions with a variety of applications, such as framing, mounting, and structural support. They are often used in construction, automotive, and electrical industries.
Aluminum Beam
Aluminum beams are structural components with a beam-like shape, providing strength and support in various applications like building construction, aerospace, and machinery.
Aluminum Angle
Aluminum angles, integral to the diverse set of aluminum extrusion types, are L-shaped profiles widely employed for corner protection, framing, and structural reinforcement across architecture, manufacturing, and transportation industries.
Aluminum U-Profile
U-shaped aluminum profiles find application in edging, framing, and protective enclosures, offering versatility and strength in diverse settings like furniture manufacturing and automotive industries.
Aluminium Ω Profile
The Ω-shaped aluminum profile, resembling the Greek letter omega, is used for specialized applications requiring unique geometries, such as decorative trims, architectural accents, and custom-designed components.
Aluminum T-Slot
T-slot aluminum profiles, an essential subset of aluminum extrusion types, feature a T-shaped slot for convenient bolt insertion, facilitating easy assembly and reconfiguration. They are prevalent in robotics, machinery frames, and modular structures, showcasing the adaptability of aluminum extrusions across various industries.