What Is Cold Forging?
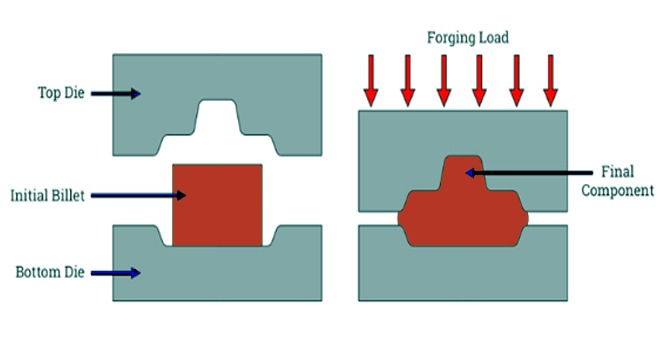
The process of aluminum cold forging involves shaping metal at room temperature using compressive forces, distinct from warm or hot forging methods. This technique, efficient for mass production, utilizes hammers, dies, or presses to deform metal bars into desired components. Cold forging results in stronger, higher-quality products compared to machining or casting, making it a preferred method for shaping aluminum components.
Aluminum Cold Forging Working Step
The aluminum cold forging process involves several key steps that contribute to its efficiency and cost-effectiveness:
Lubricant Application: Before forging begins, the workpiece is coated with a lubricant to prevent adhesion to the die and control temperature during deformation.
Feeding the Metal Coil: The metal coil is fed into the cold forging machine positioned above a die that shapes the final part, with a hammer applying force to deform the metal.
The Stroke: The workpiece is struck by a hydraulic, pneumatic, or mechanical mechanism to achieve the desired shape, with multiple strikes sometimes necessary for precision.
Part Removal: Automation processes handle part removal, reducing costs by eliminating manual handling through conveyors or robotic arms.
Post-Forging Handling: Parts are trimmed and processed for shipping directly for simple components or undergo additional die processes for complex parts, with automation facilitating the transfer of dies between stations.
Advantages Of Aluminum Cold Forging Process
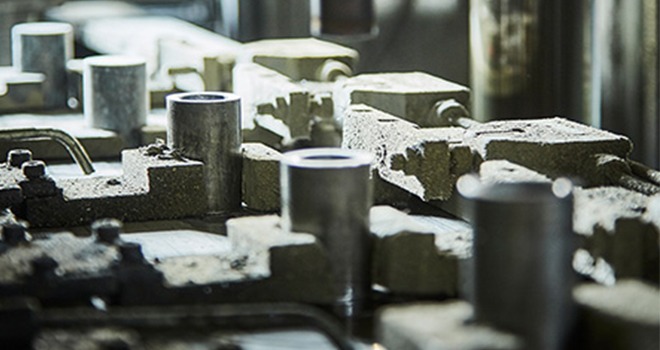
Cost-Effective
- The cold forging process eliminates the need for expensive heating equipment and intricate tooling, resulting in a 70% reduction in material use compared to machining.
- Labor costs are significantly reduced as the workpiece is completed in a single cold forging process, requiring minimal additional finishing.
Faster Production
- The cold forging process enables efficient production where components are instantly created, with automation managing loading and unloading processes.
- Metal is fed into the cold forging machine, shaped, and ejected within moments, showcasing the rapid manufacturing capabilities of cold forging.
Eliminates Negative Reactions
- Cold forging enhances metal strength and integrity, mitigating issues like porosity and fatigue.
- Parts maintain their deformed shape even under extreme stress, ensuring longevity and durability through the cold forging process.
Increased Quality and Longevity
- Cold-forged components are engineered to withstand substantial stress without reverting to their original form.
- Each part maintains precise tolerances throughout production runs, showcasing the consistency and quality achieved through the cold forging process.
Design Freedom
- The cold forging process provides greater design flexibility, allowing for the creation of complex shapes and contours in a single step.
- Unlike other methods that may require multiple operations, cold forging streamlines the manufacturing process, offering design freedom and efficiency.
High Production Output
- Cold forging processes can achieve impressive production speeds, ranging from 50 pieces per minute to over 450 pieces per hour.
- Production rates are influenced by the part’s design and complexity, highlighting the efficiency and high output capacity of the cold forging process.
What Is Hot Forging?
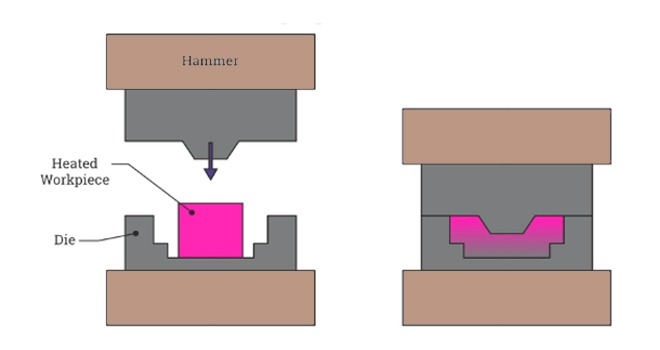
Aluminum hot forging involves the processof shaping aluminum while it is heated to high temperatures. Here are the key aspects of aluminum hot forging:
Heating Process:
- Aluminum hot forging begins with heating the dies to maintain temperature consistency and prevent premature cooling of the metal during shaping.
- Heating the aluminum increases its ductility, making it easier to deform under pressure.
Structural Changes:
- When the hot aluminum is subjected to pressure from the dies, its structure transforms into a more refined grain, leading to increased yield strength and ductility in the final product.
Critical Factors in Aluminum Hot Forging:
- Cooling: If the aluminum cools below a certain temperature threshold before shaping is complete, it may require re-heating to achieve the desired final shape.
- Tolerances: Dimensional tolerances in aluminum hot forging are generally less precise compared to cold forging due to the malleability of the hot metal.
- Dies: Custom-made dies are crucial in aluminum hot forging to meet the specific part specifications of the customer’s requirements.
Advantage Of Aluminum Hot Forging
Enhanced Material Deformation
The high temperatures in hot forging allow for maximum material deformation, facilitating the creation of intricate 3D geometries that may be challenging with cold forging
Increased Ductility
Components produced through hot forging exhibit heightened ductility, making them highly desirable for various configurations where flexibility and resilience are crucial.
Flexibility in Manufacturing
Hot forging offers greater flexibility compared to cold forging, enabling the production of customized parts tailored to specific requirements.
Excellent Surface Quality
Hot forging results in components with excellent surface quality, allowing for a wide range of finishing options such as polishing, coating, or painting to meet the exact needs of customers.
Hot Forging vs Cold Forging
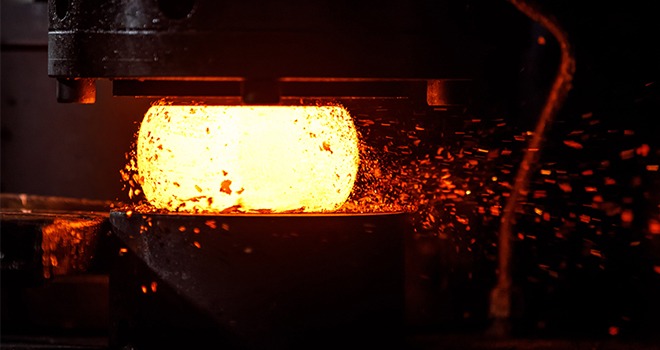
The choice between hot and cold aluminum forging processes depends on factors such as temperature requirements, the fabricator’s equipment and machining capabilities, and the types of parts being produced.
Hot Forging vs Cold Forging: Temperature
In comparing hot aluminum forging to cold aluminum forging based on temperature, the fundamental contrast arises from their operational temperatures: cold forging manipulates metals at ambient temperatures, inducing strain and stress, while hot forging entails preheating metals before molding. The pivotal temperature threshold is the austenite stage, with cold forging conducted under this phase and hot forging necessitating heating beyond it.
Hot Forging vs Cold Forging: Equipment & Machining Capabilities
When comparing hot forging to cold forging in terms of equipment and machining capabilities, the choice between these processes is heavily influenced by the available machinery and machining methods. Hot forging demands specialized furnaces or heating systems to prepare the metal for shaping, along with dies and tools resistant to high temperatures. Hydraulic presses or forging hammers are commonly used in hot forging, sometimes accompanied by cooling systems to manage temperatures after shaping.
In contrast, cold forging relies on mechanical or hydraulic presses to shape metal at room temperature. The tools and dies in cold forging are crafted to endure deformation without the need for preheating. Lubrication systems are often incorporated to reduce friction during cold forging, and additional tools for trimming and finishing ensure precise dimensions and surface quality.
The distinct equipment requirements for hot and cold forging underscore their unique operational demands. Hot forging involves shaping metal at elevated temperatures, while cold forging operates at or near ambient temperatures. Each set of forging equipment is tailored to suit the specific temperature conditions, material characteristics, and forces involved in the respective forging processes.
Hot Forging vs Cold Forging For Different Types Of Parts
The decision between hot forging and cold forging is closely linked to the specific characteristics of the parts being manufactured. Cold forging is typically preferred for simpler components with straightforward designs that do not necessitate intricate details. Products like aluminum rods, aluminum strips, and aluminum foils are ideal for cold forging processes due to their basic shapes and structural requirements.
Conversely, hot forging is generally the method of choice for parts that require precision in their intricate features. Complex aluminum products such as gears, crankshafts, and aluminum profiles, which demand fine details and tight tolerances, are often crafted using hot forging techniques. The higher temperatures involved in hot forging enhance material deformability, enabling the fabrication of parts with intricate geometries and precise specifications that might be difficult to achieve solely through cold forging.