When it comes to shipbuilding, the choice of materials is crucial for ensuring the durability, safety, and efficiency of the vessels. Two popular choices for marine applications are 3003 and 5052 aluminum. In this blog post, we will delve into the characteristics of these alloys and discuss which one might be better suited for shipbuilding.
3003 Aluminum For Ship Building
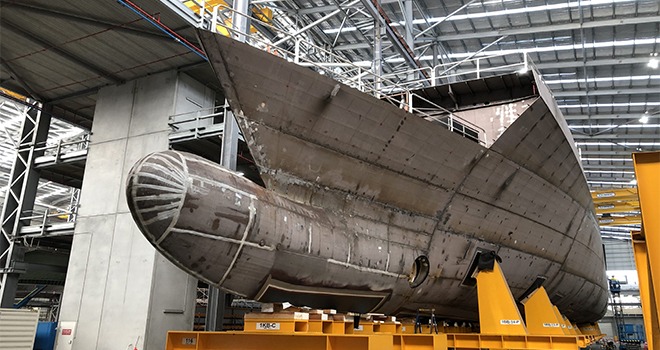
In shipbuilding, 3003 aluminum serves as a versatile and valuable material due to its exceptional corrosion resistance and formability. This alloy, known for its moderate strength and excellent weldability, finds applications in various ship components, including panels, tanks, and structural parts.
3003 Aluminum Properties
3003 aluminum properties is characterized by its moderate strength and excellent formability, making it a versatile choice for various applications. Here are some key mechanical properties of 3003 aluminum:
- Tensile Strength: Typically ranges from 110-205 MPa (16,000-30,000 psi).
- Yield Strength: Approximately 70 MPa (10,000 psi).
- Elongation: Offers good elongation properties, typically around 20%.
- Hardness: 3003 aluminum is relatively soft with a Brinell hardness of about 40 HB.
- Machinability: It has good machinability, allowing for easy shaping and fabrication.
Alloy 3003 Applications In Shipbuilding
In shipbuilding, 3003 aluminum is commonly used in various forms for different applications due to its specific properties. Here is how each form of alloy 3003 can be utilized in shipbuilding:
Aluminum Plate: 3003 aluminum plates are suitable for constructing ship panels, bulkheads, and tanks due to their corrosion resistance and formability.
Aluminum Coil: Coils of 3003 aluminum find applications in ship hulls, deck components, and internal fittings due to their ease of forming into various shapes.
Aluminum Strip: 3003 aluminum strips are ideal for trim work, edging, and small structural components within ships where corrosion resistance is crucial.
Aluminum Profile: Profiles made from alloy 3003 can be used in ship interiors for framing, decorative elements, and non-structural components that require formability and corrosion resistance.
5052 Aluminum For Shipbuilding
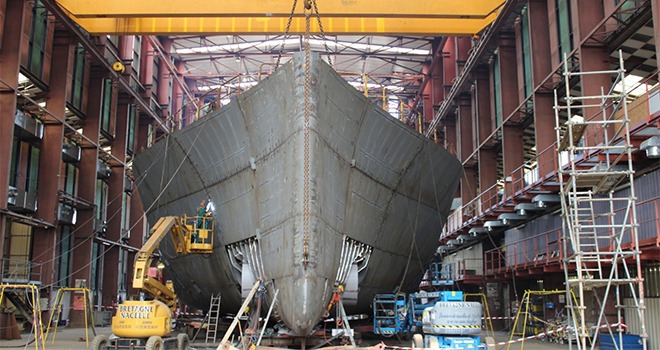
5052 aluminum stands out in shipbuilding as a highly utilized alloy celebrated for its exceptional blend of strength, corrosion resistance, and weldability, tailored precisely to meet the rigorous demands of the maritime industry.
5052 Aluminum Properties
5052 aluminum properties is notable for its balance of strength and formability, making this alloy a popular choice for various applications. Here are some key mechanical properties of aluminum alloy 5052:
- Tensile Strength: Typically ranging from 210-230 MPa (30,000-33,000 psi).
- Yield Strength: Around 150 MPa (22,000 psi).
- Elongation: Offers good elongation properties, typically around 12-20%.
- Hardness: 5052 aluminum has a Brinell hardness of about 60 HB.
- Machinability: It is considered to have good machinability, allowing for ease in shaping and fabrication.
5052 Aluminum Applications In Shipbuilding
Hull Construction: Utilized in building ship hulls for its strength, corrosion resistance, and durability, ensuring the structural integrity of the vessel.
Frames and Supports: Used for frames, supports, and structural components within the ship, providing stability and strength to the overall structure.
Deck Components: Employed for deck components such as flooring panels, stair treads, and gratings due to its corrosion resistance and longevity.
Bulkheads and Partitions: Utilized in constructing bulkheads and partitions to enhance compartmentalization and safety measures on the ship.
Internal Fittings: Applied in internal components like cabinets, fixtures, and trim for their strength, formability, and resistance to corrosion.
Piping and Tubing Systems: Utilized in piping and tubing systems within the ship for fuel lines, ventilation ducts, and other applications requiring corrosion resistance and weldability.
What Is The Difference Between 3003 and 5052 aluminum?
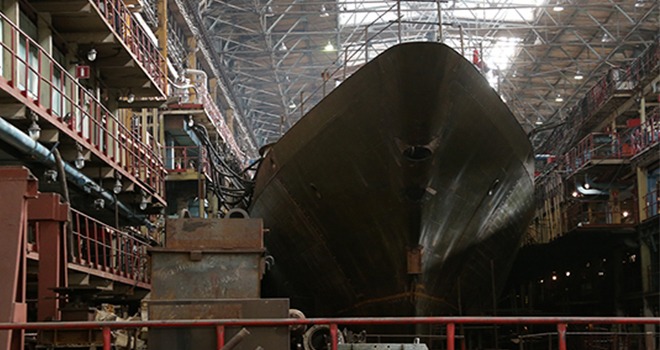
In the relm of shipbuilding, 3003 aluminum is characterized by its relatively soft nature, good corrosion resistance, workability, and weldability, along with moderate strength. On the other hand, aluminum alloy 5052 offers higher strength, superior corrosion resistance, excellent formability, and weldability. Taking 3003 and 5052 H24 aluminum as an example, the tensile strength of 5052 aluminum falls within the range of 230-280 MPa, significantly surpassing the 145-195 MPa range of 3003 aluminum.
3003 vs 5052 Aluminum: Which One Is Better?
When considering 3003 vs 5052 aluminum for shipbuilding, the choice often hinges on the specific requirements of the vessel and its components.
Aluminum alloy 5052 boasts a higher elongation strength of 150 MPa compared to 115 MPa for 3003 aluminum, indicating superior overall performance. This makes 5052 more suitable for applications demanding greater strength and durability.
In shipbuilding, 5052 aluminum sheets find prevalent use in small ships and various components like cable trays, decks, portholes, and gangways. The alloy’s enhanced strength and corrosion resistance make it ideal for these structural elements.
On the other hand, 3003 aluminum plates are commonly preferred for ship parts and anti-skid plates, particularly in areas like the anti-sinking engine room. Its characteristics of good corrosion resistance, workability, and moderate strength make it suitable for such applications where extreme strength requirements may be less critical.
Ultimately, the choice between 3003 and 5052 aluminum in shipbuilding depends on the specific needs and performance criteria of the ship components in question, with each alloy offering distinct advantages based on the desired characteristics for the given application.